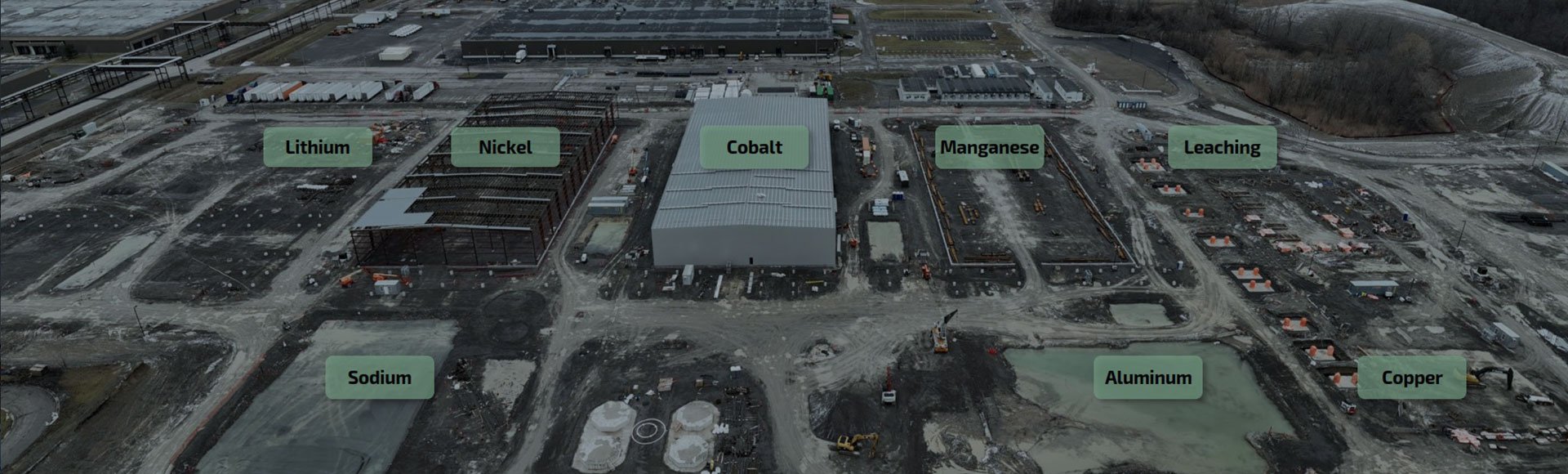
Li-Cycle Rochester Hub
Developing Li-Cycle's first commercial battery resource recovery facility
Li-Cycle
|
Rochester, New York, USA
|
2022-2024
North America's first commercial hydrometallurgical battery resource recovery facility.
Will operate at a capacity of 35,000 tpa of black mass, equivalent to 90,000 tpa of lithium-ion batteries.
At start-up, will be North America's only source of battery-grade lithium carbonate.
Challenges
- In order to meet the demand for critical battery materials, Li-Cycle established its first commercial hub facility to process recycled cathode and anode materials (referred to as "black mass") into battery-grade end products.
- The Rochester Hub represents the first commercial hydrometallurgical battery resource recovery facility to produce battery-grade materials, including cobalt, nickel, and lithium, from the black mass produced from recycled lithium-ion batteries.
- Li-Cycle needed an engineering and procurement partner with extensive experience and expertise in hydrometallurgy to develop this first-of-its-kind facility.
Solutions
- Leveraged our complex process design and large project implementation experience, alongside our deep knowledge of established hydrometallurgical processes and existing technologies to support detailed engineering efforts for the Rochester Hub.
- Engaged to provide project management services for detailed engineering, procurement, and commissioning planning.
- As of Q1 2023, completed approximately 65% of detailed engineering. Procurement is well advanced, with more than 90% of process equipment ordered.
Highlights
- The Rochester Hub represents the first commercial facility in North America to produce battery-grade lithium carbonate from recycled lithium-ion batteries.
- The Hub was anticipated to have a processing capacity of 35,000 tonnes per annum (tpa) of black mass, which is the equivalent of approximately 90,000 tpa of lithium-ion batteries.
- Through Li-Cycle's Spoke & Hub network, manufacturing scrap and spent batteries are processed in various Spoke facilities across North America. The Spokes produce black mass, which is then processed at the Hub to produce battery-grade materials.
Project Numbers
35,000 tpa in black mass processing capacity65 acres of land, including the warehouse
~US$485 million in capital costs
270,000 linear feet of piping
2.6 million linear feet of wire and cable
30,000 cubic yards of concrete
3,500 tonnes of structural steel
4,200 instruments