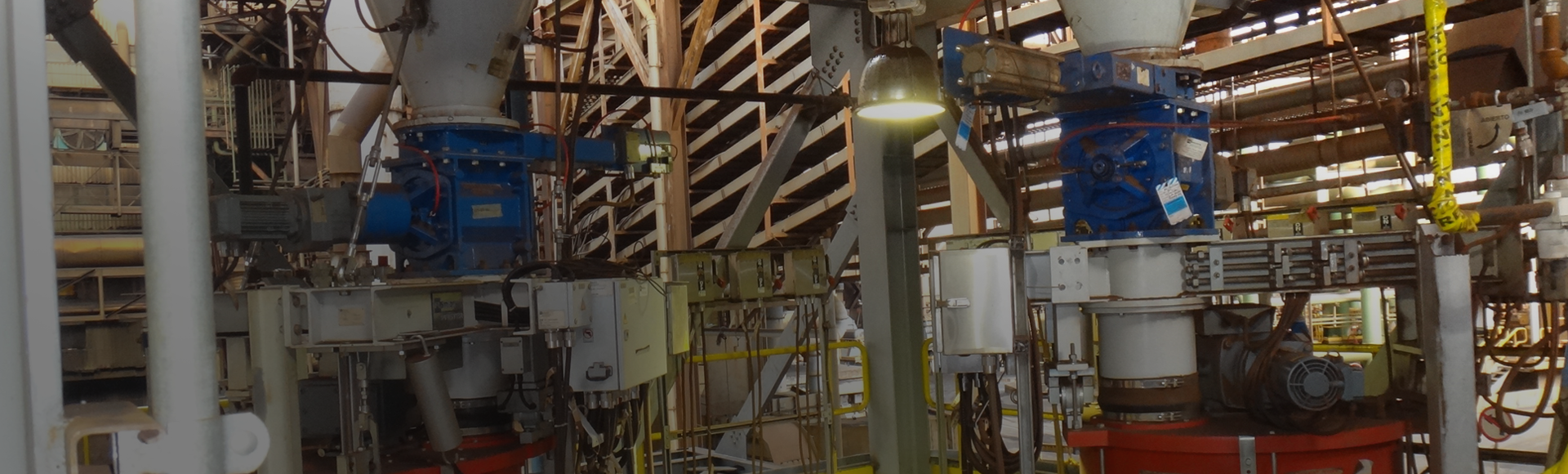
Dust insufflation project at the Cerro Matoso nickel smelter
State-of-the-art technology to optimize kiln combustion process and reduce fuel consumption
South32
|
Colombia
|
2017-2021
Challenges
- South32 has been pursuing alternative fuels and optimization of its kiln combustion process at the Cerro Matoso nickel smelter since 2008. Their goal was to reduce both operating cost and greenhouse gas emissions, with climate change as a key consideration.
- Dust is an unavoidable byproduct in nickel laterite smelters. It is typically recycled back to the front end of the Rotary Kiln-Electric Furnace (RKEF) flowsheet in the form of pellets or agglomerates with the addition of water. This results in a large recirculating dust load, energy consumption, and associated greenhouse gas emissions limiting fresh feed.
- After several studies, South32 decided to pursue dust insufflation, a new process that has been tried before but not yet successfully operated at a full-scale in the nickel industry and has seen limited overall adoption.
- Dust insufflation consists of the injection of kiln dust through the burner or separate lance, aiming to achieve a higher recovery of dust to the calcine compared to the current method.
- The project will reduce fuel consumption, increase kiln capacity, and is expected to result in a “virtuous circle” of dust recycling, by increasing its recovery and reducing the recirculation rate in their plant.
Solutions
We have supported the Cerro Matoso smelter as their engineering partner since the conceptual phase in 2008, through the study phase, and into execution.
The dust insufflation project aims to improve the calcine production and reduce fuel (natural gas) consumption through two specific initiatives:
- Injection of dry dust in kilns No.1 and No.2 through their firing hoods to reduce the amount of recycled dust in the form of agglomerates (with 25 percent moisture). This reduces the water addition and aims to achieve a higher recovery of dust to calcine compared to the current method
- Implementation of a new burner in Kiln No.2, which is expected to reduce the aeration rate through improve design and provide better flame shaping capabilities.
The project team completed the basic and detailed engineering phase, including scaling up of the concept through process modeling, careful selection of the equipment and vendors, and developing a project with the right scope and capital cost investment. This approach allowed for a successful execution, commissioning and ramp-up.
Dust insufflation in Kiln No. 1 is already in operation at a nominal rate. Construction for the new burner and dust insufflation in Kiln No. 2 is in progress and start-up is scheduled for December 2020/January 2021 during the smelter refurbishment project.
Highlights
- Dust insufflation has not been a common process in nickel laterite processing through the rotary kiln-electric furnace (RKEF) flowsheet.
- This is the first time that a plant has invested this level of technology to have precise control of the feed rates, as well as a flexible design that allows finding the optimal way to incorporate the dust into the kiln.
- The new burner, supplied by a third-party, is state-of-the-art for nickel rotary kilns replacing older technology. The assembly of different off-the-shelf solutions into a novel way to recycle dust has the potential to be used at other nickel laterite RKEF plants. The selection of the right equipment is expected to allow for precise dust dosing control.
- Commissioning support was done throughout the Covid-19 pandemic, with ongoing, regular communications between the project and client teams, and the use of virtual tools, such as Microsoft Teams.
- The project team comprised experts from both our Colombia and Canada offices.