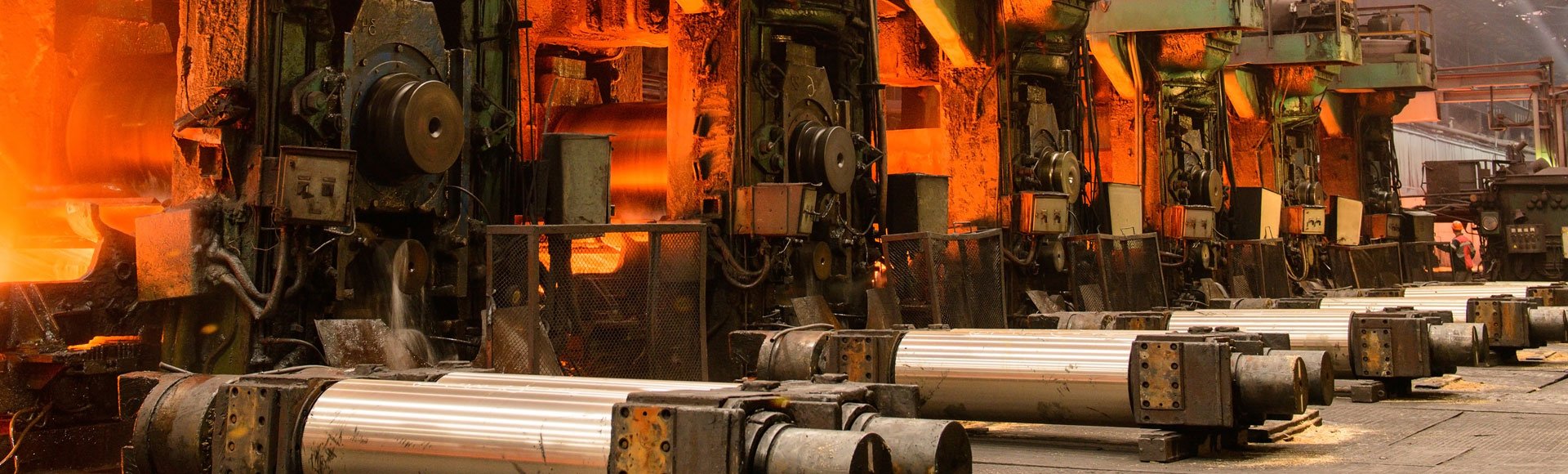
ArcelorMittal SA Vanderbijlpark FFF System Design and Supply
World-class thickness tolerances with highest mill stability
ArcelorMittal South Africa – Vanderbijlpark
|
South Africa
|
2001–2002
Over 98%
thickness tolerances within ¼ of ASTM A568M standard
No change
to finishing mill equipment
High
mill-stability improvements for rolling thin steel
Challenges
- ArcelorMittal wanted to improve the quality and reliability of hot band steel from its wide hot-strip mill in Vanderbijlpark, South Africa.
- Clients in automotive, pipe-making mills and other specialized industries needed tighter thickness tolerances from the hot rolled steel.
- The finishing mills had older, screw-down systems driven by electric motors and looper systems. Automatic gauge-control (AGC) upgrading solutions were evaluated based on performance, installation schedule, and capital expenditure.
Solutions
- With high performance comparable to best-in-class AGC systems, the Hatch Fast Feed Forward (FFF) system provided the best value to this ArcelorMittal SA hot strip mill.
- This low capital expenditure had a short implementation time, so no mill shutdown was needed.
- This maintenance-free AGC system adapts to mill conditions continuously, so it eliminated the need to change any finishing-mill equipment.
- The FFF system is able to switch between the old AGC and the existing one with a simple operator desk switch.
Highlights
- Performance of the hot-strip-mill gauge improved from thickness tolerances in the mid-80% range and less, to over 98% of thickness tolerances within the ¼ ASTM A568M standard.
- There were noticeable mill-stability improvements, with thinner steel able to be rolled with minimal amounts of operator intervention.
- Instances of torn tails were reduced by over 40%.
- A complete turnkey system, it was installed without any interruption in mill operation.
- The complete project was delivered on schedule within 12 months.
"I feel positive about the system. It is the right way to go for a mill like ours."
Project numbers
- 98% of product fell within ¼ of ASTM A568M standard-thickness tolerance.
- 40% reduction in torn tails
- 12-month implementation