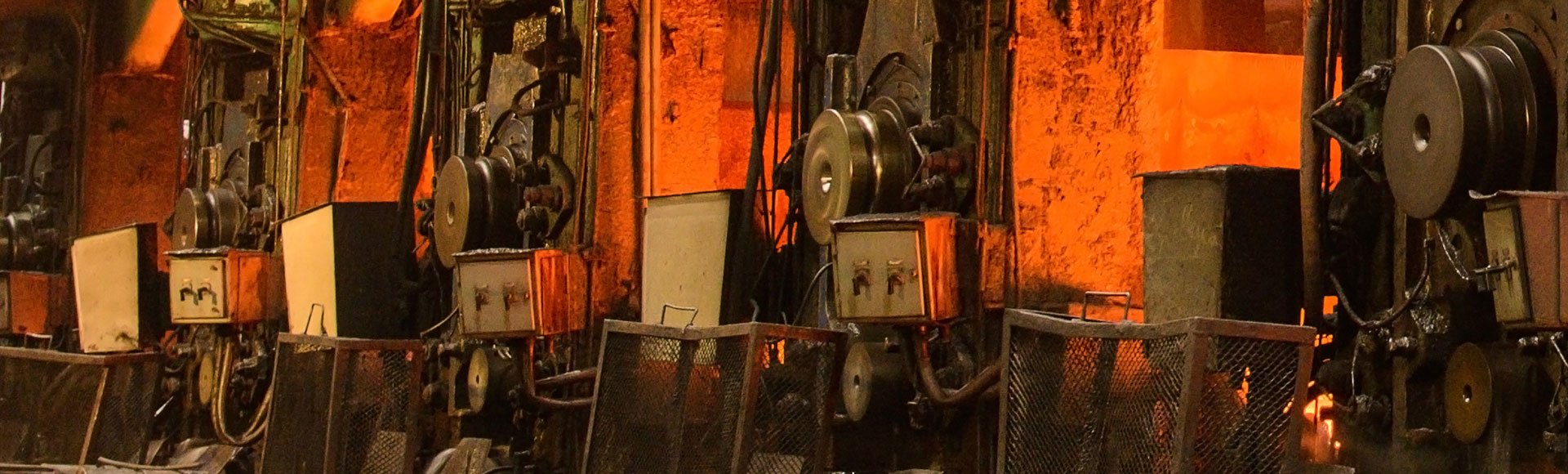
US Steel Mon Valley Works FFF System
Highest thickness tolerances at one of the oldest hot rolling mills in USA
US Steel—Mon Valley Works
|
United States
|
1995-1996
99%
thickness tolerances within 1/4 of the ASTM A568 standard
No change
to screwdown finishing mill equipment
No change
to looper finishing mill equipment
The Challenge
- US Steel wanted to improve the quality and reliability of steel production from its first generation hot strip mill (HSM) built in 1938.
- High amounts of out-of-thickness-tolerance steel from the HSM were leading to yield loss in downstream finishing processes.
- Automatic systems were being considered to control the finishing mill, including mill setup, automatic gauge control (AGC), and run-out table spray control.
- As the finishing mill had older screwdown systems driven by electric motors and older looper systems, AGC upgrading solutions were evaluated based on performance, installation schedule, and capital expenditure.
The Solution
- The Hatch Force Feed Forward (FFF) system provided the best value to the HSM in Irvin, Pennsylvania, with a high performance comparable to the best-in-class AGC systems.
- With a low capital expenditure, the FFF offered a maintenance-free AGC system that adapts to mill conditions continuously.
- The HSM was able to convert from the old AGC to the new FFF with a simple operator desk switch.
- The FFF system was integrated with other control-system models being upgraded in the same project.
The Highlights
- Hatch provided the FFF-AGC system and integrated it into the mill-control-system architecture and the new mill setup model.
- Extensive simulation was required to ensure that the FFF system would interact properly with the new setup model, drives, and mill-tracking system.
- The HSM gauge performance exceeded the project's thickness tolerances objectives of 97% within the 1/4 ASTM A568 standards.
"Significant, quantifiable performance improvements were achieved on the Irvin Plant 80” Hot Strip Mill in a cost-effective manner without major mechanical equipment replacement. Improved accuracy, repeatability, and consistency were achieved by utilizing relatively inexpensive computer systems with adaptive mathematical models."
"Beyond the initial installation, shadowing, tuning, and acceptance testing, the Hatch FFF system has been a relatively self-sustained "black box" and required minimal system maintenance."
Project numbers
98.7%-plus within 1/4 of ASTM A568 standard-thickness tolerances for thin rolled material0 maintenance required for computer models due to adaptive nature
0 learning curve start-up through preshipment testing with other systems