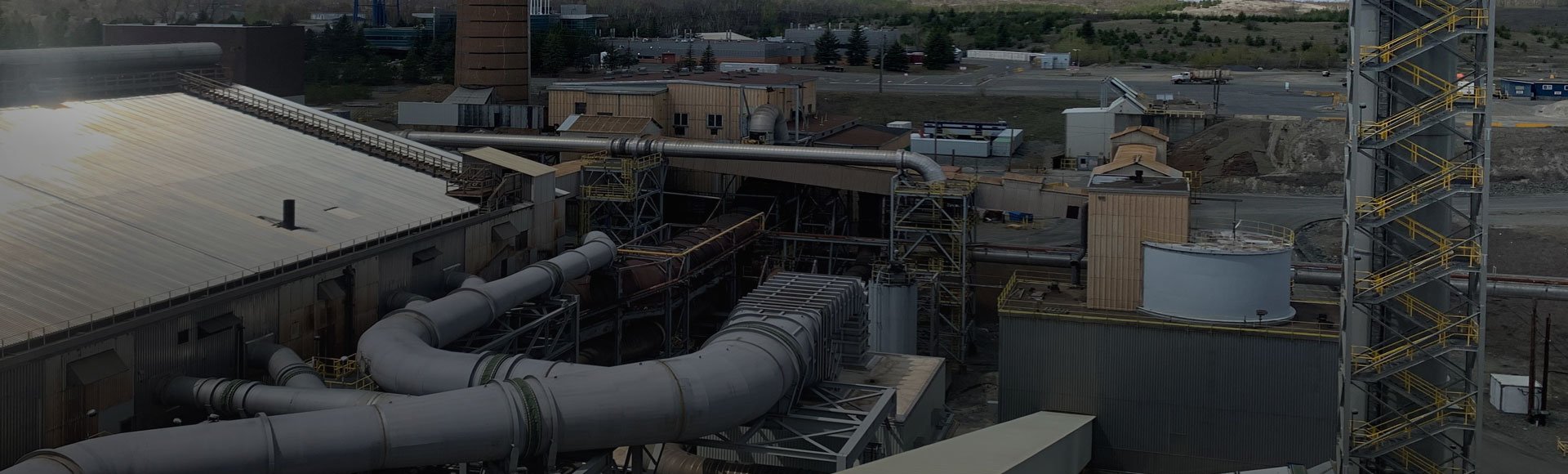
Process Gas Project (PGP) and the Particulate Emissions Project (PEP), Sudbury Smelter
Reducing sulfur dioxide and particulate emissions to improve air quality and productivity
Glencore Sudbury Integrated Nickel Operations (Glencore or Sudbury INO)
|
Canada
|
2010-2021
65% reduction in SO2
Over 1.2 million hours on-site
0 Lost-Time Injuries
16% under budget
Challenges
The Process Gas Project (PGP) Phase 1, PGP Phase 2, and Particulate Emissions Project (PEP)—a three-phase program—comprise a CAD$288 million investment by Glencore to reduce sulfur dioxide (SO2) and particulate emissions and improve productivity at the Sudbury Smelter in Ontario, Canada.
The projects were complex, brownfield executions that involved modifying virtually every major process in the smelter while maintaining 24-hour-per-day operations.
The integrated project team was required to overcome several challenges throughout the project. These challenges included:
- Maintaining 24-hour operations while modifying nearly every core process in the plant
- Achieving complex process modifications
- Governing hundreds of equipment and contract packages, and tens of thousands of deliverables
- Overcoming ground conditions that were frequently poor due to historical site use
- Addressing an equipment layout that was significantly complicated by the brownfield environment
Solutions
- We were retained by Sudbury INO to support Glencore’s response to the more stringent government-mandated SO2 and emissions-reduction requirements. The integrated project team provided full engineering, procurement, and construction management (EPCM) services for the process upgrades.
- The safe and successful execution of these services helped ensure that Smelter operations remain in compliance with the federal and provincial regulations by reducing allowable emissions of SO2 and heavy metals (nickel, cadmium, lead, cobalt).
- Meticulous implementation planning ensured that critical tie-ins could be made during short, planned shutdown windows. This approach required close coordination between our construction team and the Glencore operators who depended on our team to adhere to promised shutdown duration timelines—sometimes of only a few hours.
- We leveraged and coordinated global expertise to support the local Sudbury execution team, including specialized material handling flow modeling, acid plant design, electric furnace design, computational fluid dynamic modeling, noise abatement, process gas handling design, and machine design.
- Thorough geotechnical investigations, appropriate cost estimates, and robust foundation design were needed to ensure success with the challenging ground conditions.
- Successful execution required a high degree of field presence, including a full-time team reporting to site daily, which facilitated quick resolution of field-encountered issues.
Highlights
The integrated project team made ongoing efforts to align project and safety objectives to drive desired behaviors and project outcomes. This strong, collaborative relationship was paramount to achieving cost reductions and ultimately, project success, including:
- The projects reduced S02 measured in the community by 65%—from 40,000 t/annum total S02 emitted to 26,000 t/annum. The improved emission abatement has resulted in fewer periods during which the facility needs to curtail production due to specific weather conditions that would otherwise contribute to elevated contaminant concentrations and impact to the community.
- The Controlled Furnace Atmosphere (CFA) system used to further reduce SO2 emissions was an industry first, whereby no other engineering consultant had attempted to tie tail gas from an acid plant into an electric furnace before. Careful test work and design was needed to make this system successful.
- The combined program was executed over an 11-year period, employing over 40 different local construction contracting companies and hundreds of vendors, and resulted in over 1.2 million hours on-site over the course of the projects. The projects were completed safely, with zero Lost-Time Injuries (LTIs), and under budget.
- Continuous improvement, lessons-learned, and value improvement practices were implemented through all phases, which reduced cost and achieved a better outcome. These practices contributed to bringing the project 16% under budget without any spent contingency.
- Through rigorous project management and scheduling practices, the project did not have any impact on production at the smelter despite touching virtually every part of the operating plant. In fact, the smelter has managed to increase production since the commencement of PGP1.
Read more about how Glencore delivered environmental sustainability with the Process Gas Project.
Project numbers
The PGP project significantly reduced SO2 and metals impacts to the local community. Furthermore, reducing sulfur dioxide emissions represents another step forward in the battle to stop acid rain. The impressive results include:- A reduction of 65% in the SO2 measured in the community
- A drop in the total SO2 emitted to approximately 26,000 t/annum (from 40,000 t/annum);
- A reduction in SO2 emission intensity to achieve 0.3 t SO2 per t Ni + Cu (from 0.45);
- A reduction of 62% in the cadmium measured in the community;
- A reduction of 50% in the nickel measured in the community; and
- A reduction of 65% in the cobalt measured in the community.