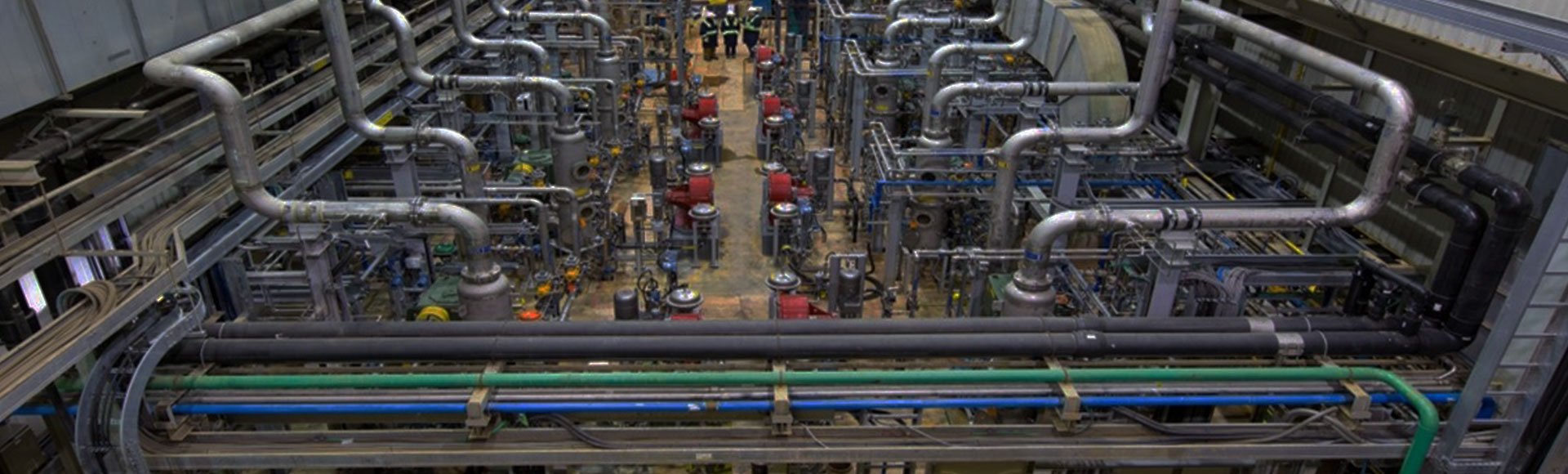
Cigar Leach Hydrogen Mitigation project
Process hazard analysis, feasibility study, basic and detailed engineering, commissioning
Orano Canada Inc. (AREVA Resources Canada Inc.)
|
Saskatchewan, Canada
|
May 2013 – September 2014
15-month condensed schedule from initial PHA to commissioning.
Leaching circuit upgraded to process high-grade uranium ore.
Project completed on-schedule and on budget with an excellent safety record.
Challenges
- Orano’s McClean Lake facility is an existing uranium processing plant located in Northern Saskatchewan, Canada.
- As a result of changing the uranium ore feed to a high-grade material, Orano’s laboratory testing program identified the potential risk of hydrogen evolution during leaching.
- As a consequence to hydrogen evolution, Orano was concerned that the existing leaching equipment may not be equipped with adequate safeguards to manage the hydrogen, which posed a safety risk.
Solutions
- Approached by Orano to assist with evaluating the design modifications for the McClean Lake leach circuit to ensure that it would be able to safely process the Cigar Lake high-grade uranium ores.
- Hatch’s High-Pressure Metallurgy (HPM) practice commenced support with a process hazard assessment (PHA) review with the McClean Lake operations team, including process, operations, maintenance and engineering members.
- The project required several trade-off studies to determine the best solutions to repurposing the existing process equipment and resolving the hydrogen concern.
Highlights
- The results of the PHA resulted in HPM completing a feasibility study (FEL3) and immediately progressing to basic engineering and detailed engineering (FEL4) for the proposed circuit upgrades.
- Commissioning of the upgraded leach circuit was achieved in September 2014.
- This was a brownfield, schedule-driven project that included repurposing of existing process equipment, limited space for new process equipment, demolition of existing infrastructure, and effective design considerations to help optimize the overall schedule.
- The modifications to the process equipment included upgrading seven leach vessels with new agitators to provide adequate solid suspension and blending; design enhancements to enable slurry feed forward control; installation of hydrogen and oxygen analyzers; installation of dilution air and vent gas exhaust systems; installation of emergency back-up systems including repurposed diesel generators, uninterrupted power supply, and a passive nitrogen purge system.