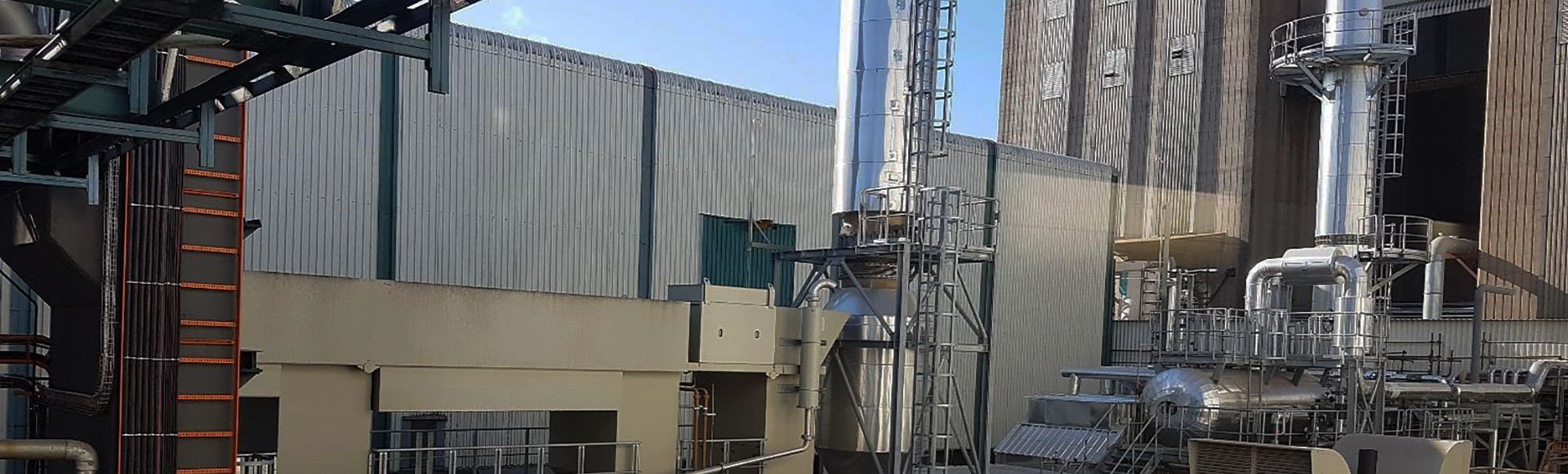
Rosslyn Brewery Cogeneration Plant
Maximizing production with a more efficient and reliable source of energy
Anheuser-Busch InBev
|
South Africa
|
2016-2018
Cogeneration plant with a guaranteed efficiency of +88%.
Zero LTI in 164,000 hours.
Largest brewery in South Africa.
Challenges
- AB-InBev’s Rosslyn Brewery is the largest brewery in South Africa and is key to the company’s Southern Africa production targets.
- Brewing is an energy intensive process requiring large quantities of both electricity and steam—a reliable source of energy is essential.
- Ongoing load shedding was affecting their operations.
- Full integration with the existing brewery was required in terms of steam, hot water, and electricity generation with minimal impact on production.
- The project involved extensive brownfield work due to wide-ranging integration challenges.
- The 850-m gas pipeline included a 120-m horizontal directional drilling (HDD) exercise near a rail line, two road crossings, and numerous water supply lines and fiber and electrical cables.
Solutions
- Conducted an engineering study of options to provide a source of in-house electrical generation while optimizing the brewery’s steam production process to ensure security of supply. The study identified attractive benefits if they installed a natural gas-fired combined-heat and power (CHP) plant.
- Based on the outcome of the study, AB-InBev extended Hatch’s appointment to provide EPCM services to design, construction manage, and commission the entire CHP plant.
- The installation of the CHP plant required the installation of a new, high-pressure, underground gas supply pipeline from the existing Sasol natural gas line to the brewery, a high-pressure metering station, the redesign of the electrical reticulation system to allow for a combined electrical feed from the municipality, the gas turbine generator, an additional diesel generator for black start scenarios, and future allowance for solar PV panels.
- We designed the hot water recovery system, including the complex functional and control system.
- We developed the specifications for the CHP plant (gas turbine and heat recovery steam generator), a new 35-bar natural gas pipeline, electrical switch gear, and construction packages.
Highlights
- Capital investment will be paid off in less than four years.
- Using a similar amount of natural gas that was used in the gas-fired boilers to generate 4 MW of electricity and the same amount of steam.
- Implementation of the project provides AB-InBev with improved efficiency in reduced energy requirements.
- Plant personnel were trained by Original Equipment Manufacturers to gain an understanding of the technologies and practical experience control and maintain the plant.
Project numbers
- 8 principal contractors and CHP suppliers on site
- 163,842 total project man-hours
- 0 Lost-time injuries
- 4 MW of electrical power using a gas turbine
- 28.5 tonne/hour of saturated steam generated
- 41 tonne/hour of hot water
- 14 months of construction and commissioning work