Challenges
Keeping mechanical and structural assets in good working order is a constant challenge in metallurgical, energy, and infrastructure industries. Assets eventually deteriorate or become damaged during operations and must be retrofitted or replaced to maximize productivity and ensure continuous and safe production. Comprehensive inspection and monitoring techniques are needed to extend the service life of mechanical and structural assets and optimize maintenance schedules and productivity.Non-Destructive Testing (NDT) techniques and monitoring systems can be used to assess the condition and deterioration of mechanical and structural assets without intrusive instrumentation or damage to the assets. In many cases, NDT techniques can be applied without disrupting normal operations.
NDT has a wide range of benefits, including accident prevention, facilitation of maintenance planning, and optimization of efficiency and profitability. Used regularly, NDT contributes to safer, more reliable assets, and greater profits for the companies that own them.
Capabilities
Acousto Ultrasonic-Echo (AU-E)
This Hatch-patented technique measures the thickness and condition of refractory linings in operational metallurgical process vessels. AU-E can be performed during vessel operation without disrupting the production schedule. It can detect refractory conditions such as remaining thickness, build-up thickness, and chemical alterations such as metal impregnation, metal penetration, hydration, and oxidation. Periodic AU-E measurements can assist the planning of repair and optimize refractory lining campaigns.
AU-E on-site inspection
​
Low Frequency Pulsed Ultrasound
This system measures the wear and deterioration of cooling staves in blast furnaces. LFPU can determine the remaining stave thickness from the cold face of the furnace shell while the furnace is fully operational. It is a more advantageous solution to destructive drilling and conventional ultrasonic rod thickness measurements. LFPU is flexible and can measure any location of the stave, while the conventional techniques can only measure locations where ultrasonic rods were installed.
​
Stray Current Measurement
This system allows the detection of cracks or initiation of cracks on rails. Early detection of cracks can ensure timely repair and maintenance to ensure rail safety. The stray current measurements are fast and can be done overnight while the railroad is not in use.
Stray current railway inspection
Furnace Integrity Monitoring System
Our patented technique prevents and provides early warning of structural failures and run-outs in metallurgical furnaces. A system of sensors, it detects and maps acoustic emissions that can be caused by refractory movement and changes in the vessel integrity.
FIMS for real-time continuous furnace integrity monitoring
Radar feed-level measurement
This automatic feed level measurement system was developed by our experts based on electromagnetic waves. The patented system can accurately and continuously measure the top level of the concentrate or feed bank in metallurgical furnaces. Real-time feed-level measurement allows furnace operators to optimize the smelting process, reduce energy consumption, prevent premature damages of the furnace roof, and thus, can reduce maintenance costs, reduce furnace downtime, and increase profitability.
​ ​
ElectroDAR
This patented system determines the tip position of electrodes in electric arc furnaces. It uses electromagnetic wave signals to continuously measure the electrode tip location during furnace operation. The real-time electrode-tip-position measurement allows operators to maintain the desired power input, increase furnace efficiency, and produce a lower cost, higher quality product.
Taphole acoustic monitoring (TAM)
This Hatch-patented system monitors directional drilling, lancing, and tapping operations in metallurgical furnaces. TAM detects and locates acoustic emissions during these operations. Any directional lancing, and uneven wear of the taphole refractory lining is mapped as significant AE activities in real-time to provide the condition assessment of the tapholes. TAM can be used to enhance safe operation of tapblocks and optimize taphole campaign life.
Conventional NDT
We also perform conventional NDT, including ground penetrating radar, impact echo, infrared thermography, magnetic particle inspection, ultrasonic inspection, and liquid penetrant inspection, as well as structural health monitoring by acoustic emission technique. Our conventional NDT services are applicable to any infrastructure, including industrial assets, bridges, building, nuclear power plants, hydropower plants, oil and gas infrastructure, pipelines, metallurgical vessels, and assets. We customize solutions to suit site conditions and client requirements. Contact us for more details and let us assist you on customizing a solution that is right for you.
I. Ground penetrating radar (GPR):
This Hatch-patented system monitors directional drilling, lancing, and tapping operations in metallurgical furnaces. TAM detects and locates acoustic emissions during these operations. Any directional lancing, and uneven wear of the taphole refractory lining is mapped as significant AE activities in real-time to provide the condition assessment of the tapholes. TAM can be used to enhance safe operation of tapblocks and optimize taphole campaign life.
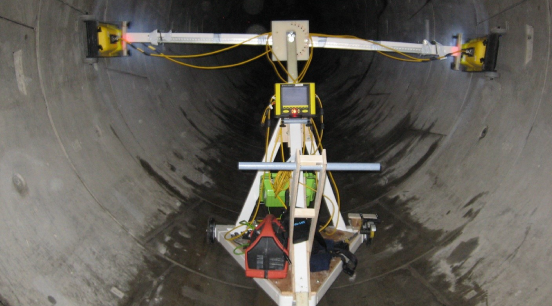
Hatch tailor-made a GPR system for the inspection of sewer pipes.
II. Infrared thermography:
For more detail condition assessments, we often use a few NDT techniques to narrow down the problematic areas, verify the findings and increase the certainty of the test results. Infrared thermography is often selected as a tool for this purpose.
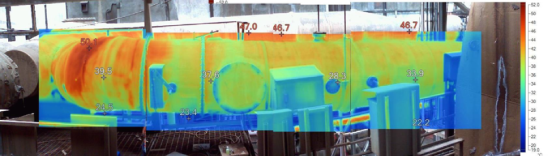
Infrared thermography inspection.
III. AE monitoring for leak detection:
Our AE monitoring system is used for continuous real-time monitoring of structures. We applied the system for the detection of acid leaks in metallurgical plants, and water leaks in pipes. This system can also be applied to infrastructure, such as cable stayed and suspension bridges, to detect initial signs of cracks on the tendons and cables.
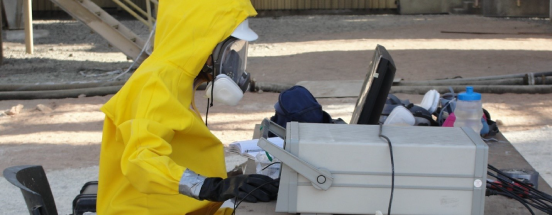
AE monitoring for acid leak detection.