Driving sustainability and cost savings through waste heat recovery in industrial applications
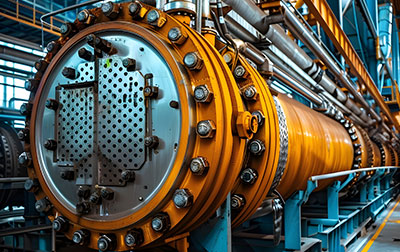
By capturing and repurposing energy that would otherwise be lost, WHR not only reduces emissions but also generates significant cost savings, enhancing profitability and competitiveness.
For existing facilities, WHR serves as an effective transitional measure, while for new projects, it provides an opportunity to embed energy efficiency from the outset.
Supporting the transition in existing operations
For facilities operating legacy equipment, the road to decarbonization is often paved with challenges: regulatory pressures, rising fuel costs, and the need to maintain reliable operations. WHR offers a cost-effective solution, enabling industries to bridge the gap between current processes and future sustainability goals by harnessing wasted energy.
The four key advantages of WHR for existing operations are:
- Lower operating cost and improved efficiency – By recovering and utilizing waste heat internally, fuel consumption can be reduced and efficiency improved, delivering substantial cost savings. Moreover, for facilities located near district heating networks or utilities, excess heat can be exported or converted into power, as additional revenue streams.
- Cost-effective emissions reduction – By consuming less fuel, CO2 emissions can be avoided, without the need for a complete overhaul of assets and with many of these projects attracting government subsidies to reduce capital cost, project feasibility can be significantly enhanced.
- Minimal operational disruption – Our WHR solutions are engineered for minimal disruption to existing operations. These systems minimize downtime during implementation, ensuring continued operations while delivering measurable benefits.
- Robust business case – Lower operating cost, reduced emissions and the potential to export useful energy can combine to provide strong justification for delivering positive, triple bottom line business outcomes.
Maximizing efficiency in new projects
When incorporated at the design stage, WHR systems provide new projects with a foundation for exceptional efficiency. By capturing and utilizing waste heat, these systems reduce energy demand, lower operational costs, and as a result lowers overall carbon intensity.
The key advantages for new projects are optimizing energy use and future-proofing sustainability. Designing facilities to incorporate WHR systems maximizes energy efficiency from day one, minimizing fuel costs over the project lifecycle. Integrating WHR at the outset is future proofing sustainability; it aligns new projects with stricter environmental regulations and enhances resilience in a decarbonizing economy.
WHR: a practical and proven pathway
While WHR is not a new concept, its relevance has grown significantly as industries seek actionable pathways to reduce their carbon footprint and improve efficiency. Our dedicated WHR team develop and deliver advanced ECOSTAT solutions and proprietary ECOFLOW heat exchangers, tailored to meet the diverse needs of industries, offering robust, reliable, and efficient heat recovery technologies that integrate seamlessly into various industrial processes.
In part two of this blog series, we will provide further details of our tailored energy solutions.
We bring a wealth of experience to WHR industrial processes, having delivered over 200 successful implementations worldwide. From feasibility studies to end-to-end implementation, our solutions are tailored to meet the specific needs of each client, ensuring seamless integration, measurable results, and long-term reliability.
Contact us to start your WHR journey today!
Our insights share the latest innovations and ideas that are helping to solve our clients' biggest challenges.