Navigating the waves: Steel Industry's Raw Material Challenges in the Green Transition
Tons of challenges
When looking at increasing demand for steel, Hatch research shows that the industry’s adaptation to low-emission technology will have a significant impact on raw materials. Our models indicate a 10% increase in steel demand from 2024 to 2040. To accommodate that, the production of “DR grade” iron ore pellets and scrap steel used in low-emission steelmaking will need to increase substantially.
Assuming a gradual adoption of low-emission technologies over that period, the increase in annual demand for DR pellets will likely balloon by 200 million tons, with scrap demand increasing by 230 million. To put that in context, annual DR pellet production increased by 100 Mt in the last 17 years, now the iron industry must find double that annual volume—200 Mt in the next 17 years.
This then leads to the increased pricing of DR pellets, which is driven by the cost of improving ore quality, the cost of pelletizing, and market demand. Over the last three years, the premium has gone up and the increases are expected to continue. The increasing premiums have a two-fold impact. One, it incentivizes more resources to be brought to the market. Two, it increases the cost of decarbonization.
As for scrap, its use in EAFs to produce steel grades currently made via the blast furnace route will be limited by the cleanliness of the scrap, meaning impurities such as copper, tin, and vanadium that enter the scrap in the collection process must be a kept at a minimum level as they cannot be removed elsewhere in the steelmaking process. This new and ever-growing demand for high-quality scrap decreases its availability—and it’s already becoming scarce as steel is continually recycled—ironically, one of its biggest attributes. What this means for steel producers is that relying entirely on scrap as a feed for steel production to replace high purity blast furnace iron is going to get more challenging. Some steel producers are already acquiring scrap facilities, which means the supply of scrap will become even more limited and costly for other steelmakers.
It is essential that the steelmaking leadership grasps the magnitude of this situation; that they become laser-focused on iron feed units such as DRI and scrap. Globally, there is plenty of DR grade iron ore; however, it is unequally distributed geographically. Understanding where it is, and how to access it will drive investment in low-emission steelmaking technology.
Clearly, a dramatic change is needed—and in fact is already occurring—in the industry. And it’s coming in three waves of development.
Waves of the future
The first wave is already washing over the industry. It is a capital-intensive rush to market, driven by technology and the adoption of DRI and EAF. This will soak up DR grade material and scrap, drive up premiums, and force investment in the limited amount of resources available.
The second wave involves investing in both DRI facilities and securing upstream access to high-quality iron ore that is of the right grade.
Waves one and two are expected to take five to seven years. Europe and North America are in the best positions to take full advantage of the first two waves as they have a combination of an availability of feed material, utilities that use green energy, natural gas, and hydrogen, and government support in terms of grants and policy. Conversely, many regions, such as China, Southeast Asia, and India will continue to build blast furnaces for the foreseeable future until regulations start to become more stringent, thereby forcing them to decarbonize.
Wave three is where things get interesting. It requires the industry to determine how to deal with lower-quality iron-ore sources that play a large part in the volume we have now. These producers provide feed to India and China, and to many of the steelmakers that use blast furnaces globally. At some point, the industry has to imagine a world in which those large-volume blast furnace producers start to decarbonize. When they do, it may pose a risk to many iron ore suppliers and places around the world that need to transition or face an existential crisis.
Still, the future seems bright. Iron ore producers are actively investing in ways to upgrade low-quality reserves to DR pellets and/or implementing novel ironmaking technologies. Currently, there are approximately 40 to 50 different types of novel ironmaking technologies in different stages of development. Success will require partnerships between iron ore producers, steel manufacturers, and technology developers to get these to market and scaled for massive production volumes.
The road ahead
Hatch is addressing many of these challenges by investing heavily in its Continuous Reduced Iron and Steelmaking Process (CRISP), a large furnace for the efficient melting of DRI (incl. BF grade) and scrap for conversion to iron or steel.
Regardless of which decarbonation path is taken, steel producers should know that the industry is no longer just about managing operations efficiently. It’s now about developing new technologies and implementing projects to transform operations at a scale not seen since the transition from open hearth to basic oxygen steelmaking. The future of the steel industry hinges on innovation, collaboration, and a steadfast commitment to sustainability. By embracing these changes, the industry will navigate the waves of transformation and emerge stronger, greener, and more resilient.
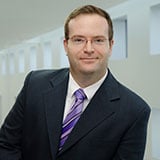
Matthew Cramer
Global Director, Advisory
Matthew has spent the last 15 years working in pyrometallurgical and other heavy industry environments as an operational leader and consultant. He is passionate about implementable risk reduction programs and strategies and a staunch supporter of safety initiatives and their benefits. By working hand in hand with Clients Matthew is focused on creating a better world through the development and execution of fundamental changes to their operating models. Matthew has worked with Clients across North and South America, Europe, China and Africa.