The future of railway maintenance: Optimizing condition monitoring and assessment for reliability and efficiency
Many railway networks worldwide are more than 50 years old. Over time, the natural wear and tear caused by constant usage, coupled with environmental factors, has led to significant deterioration of key railway assets. Historically, maintenance strategies have focused on reactive measures—addressing issues only once they arise and failures occur. While this may have been sufficient in the past, reactive maintenance today is proving to be costly, inefficient, and disruptive. Unplanned breakdowns and emergency repairs result in lengthy downtimes, reducing the availability of critical rail lines and negatively impacting overall logistics and the economy.
As a result, the railway industry is undergoing a paradigm shift toward proactive maintenance. This approach is built on modern technologies that enable real-time monitoring of railway infrastructure and predictive analytics to anticipate future failures—a transition that’s not just about preventing breakdowns but about optimizing maintenance schedules, reducing costs, and extending the life of railway assets.
Condition monitoring and IoT
A key aspect of this transformation is condition monitoring, involving the continuous tracking of railway assets like including tracks, rolling stock, and overhead equipment. IoT sensors, GPS mapping, and diagnostic tools enable maintenance teams to gather extensive real-time data. These sensors monitor track geometry, temperature changes, and vibration patterns, allowing early detection of wear and tear. This data informs maintenance strategies, decisions and optimizing resource deployment.
For example, IoT sensors on rail tracks can detect slight misalignments or material fatigue early, alerting central systems when maintenance is needed. Big data analytics help the railway industry process vast amounts of information to uncover hidden trends, enabling operators to predict failures before they affect operations.
Innovative technologies
One of the most promising developments in proactive maintenance is the use of Remaining Useful Life (RUL) modeling. This concept predicts the lifespan of key assets based on their usage, environmental conditions, maintenance history, and historical performance and uses advanced data analytics to estimate when an asset, such as a section of track or a locomotive/wagon component, will likely require repair or replacement. By forecasting the future condition of these assets, maintenance teams can schedule interventions during planned downtimes, minimizing disruptions and reducing the cost of emergency repairs.
Figure 1: Graphical illustration of Monte Carlo Simulation Model showing input variables and outcomes
An excellent case of the advantages of RUL modeling can be seen in track component management. Continuous pressure from heavy haul trains results in gradual wear on the tracks, especially when braking or acceleration occurs. By taking these stress points into account, RUL models can forecast when a specific track section is nearing the end of its lifespan, enabling maintenance teams to schedule precise repairs at optimal times. This predictive maintenance approach prolongs the lifespan of railway components and ensures smoother and safer train operations.
Unmanned aerial vehicles (UAVs), or drones, are improving maintenance efficiency. With high-resolution cameras and thermal sensors, drones can swiftly inspect railway tracks, bridges, and overhead equipment. These inspections are quicker, safer, and more cost-effective than manual ones, reducing the need for workers to be on tracks or at heights. UAVs can identify hidden defects like micro-cracks in steel or early signs of rust, enabling operators to fix issues before they escalate, preventing costly repairs or failures.
The advent of artificial intelligence (AI) is revolutionizing the railway maintenance industry with systems that are capable of processing enormous volumes of data from sensors, historical records, and environmental factors to forecast asset performance and identify potential risks. By interpreting weather patterns and their impact on track wear, engineers can adjust maintenance schedules proactively to avoid weather-related failures. And by accurately predicting the effects of various freight loads on rolling stock, operators can optimize load distribution and minimize wear on wagons and locomotives, increasing system resilience.
Supported by these new technologies, proactive maintenance is fundamentally altering the way railway systems operate. Condition-based maintenance and preventative maintenance have proven far more effective than reactive strategies. Condition-based maintenance relies on the continuous monitoring of assets to detect degradation as it happens, while preventative maintenance involves scheduled inspections and repairs to prevent failures before they occur. Both approaches reduce costs, improve safety, and ensure that railway systems remain operational and efficient over the long term.
A multidisciplinary approach
Effective railway maintenance is inherently interdisciplinary, involving civil, mechanical, electrical, and logistics industrial engineers. Civil engineers handle track upkeep, mechanical engineers ensure rolling stock reliability, electrical engineers manage signaling and power supply, and logistics specialists coordinate activities to minimize schedule disruptions. This approach ensures cohesive network functioning and prevents isolated issues from escalating.
At Hatch, we’ve seen firsthand how the modernization of railway systems can improve operational efficiency and the broader socio-economic landscape. This expertise translates directly into our work on heavy haul systems, where proactive maintenance strategies can yield similar benefits.
Whether implementing IoT sensors, using AI for predictive maintenance, or employing drones for inspections, our team is equipped to help you choose the most suitable solutions for your specific railway challenges. Contact us to find out how our extensive expertise in incorporating modern technologies into older infrastructure can ensure that your railway system remains safe, efficient, and dependable.
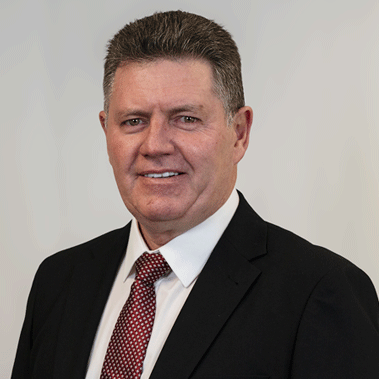
Bennie Vorster
Regional Director, Transit, AIM
With over 27 years of experience in railway engineering, Bennie Vorster excels in strategic and capacity planning, logistics, rail and yard design, train operations, rolling stock maintenance, feasibility studies, project management, business process re-engineering, and rail simulation. He is leading a unique and dynamic rail & transit team in the Africa, India and Middle East region that is supporting clients globally from the Hatch Johannesburg office.