Challenges and opportunities for the adoption of autonomous hauling trucks in mining
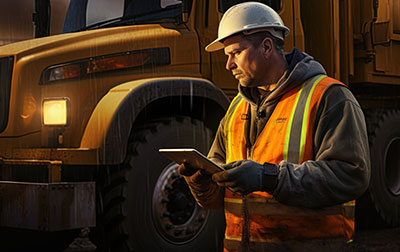
The adoption of each of these transformative technologies entails addressing a series of challenges with a high level of preparation and planning. The automation of haulage fleets, otherwise known as autonomous haulage systems (AHS), seems to be the chosen path for much of the mining industry, particularly in Latin America, with mining companies such as Codelco (Gabriela Mistral), Anglo American (Quellaveco), Vale (Brucutu), BHP (Escondida & Spence), Teck (QB2), and AMSA (Centinela) leading the way.
This technology has shown the potential to deliver higher levels of utilization in a haulage fleet (e.g., +700 hours/year/truck increase1). However, to achieve the desired key performance indicators (KPIs), such as reduced costs, improved productivity, and higher safety, it is necessary to overcome a series of challenges:
Cost
While AHS projects can result in reduced fuel consumption, increased tire lifespan (exceeding 8,000 hours2), and reduced maintenance costs; there are new costs generated from their implementation, that oddest in some way the benefits, including manufacturer licensing fees, new specialized roles required, increased road maintenance activities, cybersecurity, improved telecommunications at site, and server costs. Because multiple items could affect the project's performance, it is necessary to be precise in estimating associated costs.
Productivity
The speed of autonomous trucks is often lower than that of manned/conventional ones (e.g., -15%3). While this is partly due to safety conditions programmed for truck movement, there are also other operational factors. Primarily, interactions with other manned equipment often cause AHS vehicles to stop when the manned equipment enters the established autonomous vehicle’s safety bubble. Similarly, inert obstacles that could easily be overcome by truck operators (such as boulders) cause autonomous vehicle stoppage when not previously identified as part the vehicle’s route.
Safety
Implementing new safety processes and protocols involves a deep cultural transformation to increase risk awareness associated with autonomous technology. It requires establishing a solid operating model and adequately training personnel in the use and maintenance of this technology. One of the main safety challenges is the interaction with the vehicle bubble, which is designed to stop the system in several situations to overcome technology limitations and minimize the probability of accidents.
To facilitate and accelerate the successful adoption of these technologies and overcome these challenges, it is essential to address the following action levers:
- Clarity on the objectives to be achieved with these new technologies
It is crucial to establish the expectations of implementing an autonomous system. The experience of AHS adopters has shown, improving cost efficiency and productivity presents significant challenges. It is important to have a deep understanding of the implications of incorporating this new technology. Dynamic simulation is a tool capable of incorporating various operational variables when estimating potential benefits. In this way, one can increase confidence in the estimated business case by clearly establishing baseline benefit KPIs and setting expectations for improvement aligned with specific operational conditions. - Thoroughness in defining the technical bases for equipment acquisition
Transforming the original equipment manufacturer (OEM) from a supplier to a strategic partner is a fundamental aspect of this comprehensive approach. By working closely with the OEM from the early stages of the acquisition, mining companies can leverage the manufacturer's knowledge and experience to develop detailed technical specifications that align with their operational and strategic needs. This involves considering aspects such as interoperability with existing mine systems, integration with IT and communications infrastructure, and adaptability to future technology updates. In this way, a comprehensive features assessment of the candidate technologies is ensured before making decisions during the acquisition process. - Development of a balanced contract between partners
Contracts must clearly and precisely define the roles and responsibilities of each party involved in system implementation and operation. This includes specifying strategic partner responsibilities in terms of supply, installation, configuration, commissioning, technical support, and service levels. Contracts must clearly establish performance criteria and objectives to be achieved with the implementation, as well as monitoring and evaluating mechanisms to measure compliance with these objectives over time. They must also include clear provisions to mitigate and manage the risks identified in advance through collaboration between the strategic partner and the owner. - Mining planning with a comprehensive understanding of autonomy incorporation
The development of a greenfield project is the ideal time to introduce autonomy as retrofitting conventional operations (i.e., brownfield) to autonomy involves numerous considerations and challenges that prevent a smooth transition between technologies. Mining plans must not only consider appropriate geometric parameters for autonomous systems in the pit design, but also incorporate stages of gradual implementation to ensure a proper transition to the new technology. Initially, it is prudent to establish a period where autonomous vehicles operate on specific haulage routes allowing personnel to become familiar with the technology and make appropriate infrastructure adjustments while risks remain controlled. Subsequently, the technology is gradually scaled while being integrated into the entirety of mining operations, with a priority on flat routes over slopes. It is also necessary to facilitate the integration of future technologies by reserving spaces for battery storage and trolley system infrastructure. - Robust and optimized IT/OT systems for autonomous vehicle operation
It is crucial to anticipate events that may affect the autonomous system operation, such as communication loss due to solar flares, cyberattacks, and sensor obstruction due to environmental conditions. Several mitigating measures, such as early warning systems, are required. The growing reliance on digital systems also increases vulnerability to cyberattacks, with cybersecurity costs having tripled since 20154. This underscores the need for comprehensive management in this area. Conversely, the implementation of AHS can increase the overall level of instrumentation in the hauling fleet, enabling improvements in operational control and condition monitoring for predictive maintenance. - Early integration of roles with expertise for AHS systems
Organizations must prioritize the identification of gaps in their current capabilities regarding AHS operation. They must develop strategies to acquire this knowledge, execute through internal training programs, and initiate recruitment campaigns for qualified personnel. This proactive approach mitigates the inherent risks in the startup and operation phases by facilitating a successful implementation and accelerating the capture of the technology's potential value. - Change management as a key enabler to autonomous system adoption
The transition to autonomous trucks involves aligning management in terms of governance and organizational culture to effectively adopt autonomy. This process consists of redesigning processes, adjusting the operating model, and establishing new performance indicators, which affect the roles and capabilities required within the company.
Hatch has the experience and specialists to provide comprehensive support for the introduction of AHS technology and to accelerate its adoption and value capture. Hatch provides simulation tools to predict the performance of autonomous systems based on real conditions and right-sizing achievable metrics, and supports implementation and change management to attain improved and realistic KPIs.
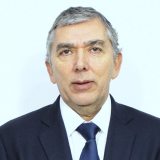
Rafael Valenzuela
Mining Consultant, Mining
Rafael is a mining executive with over 29 years of experience in planning and operations in the Gran Minería del Cobre in Chile and has participated in the evaluation and start-up of greenfield and brownfield mining projects. He has led the formation of teams in the areas of geology, geotechnics, metallurgical processes, and mining planning. He has over 10 years of experience in the first implementation of autonomous transport system technology at Minera Gabriela Mistral, participating in technical-economic evaluation, contracts, and mining operations, implementing improvements in mining design and operational performance of the autonomous system. Currently, he integrates and develops his experience in mining consultancies.
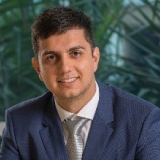
Tiago Becker
Senior Business Analyst, Advisory
Tiago Becker is part of the Advisory team in Hatch’s Lima-Peru office. Specializing in the mining sector, his hands-on experience focuses on digital transformation, strategic planning and decarbonization. His track record includes spearheading projects in these domains regionally, leveraging his expertise to drive operational efficiency and sustainable practices. Tiago's pragmatic approach and deep understanding of industrial processes make him an asset in navigating complex challenges and delivering tangible results.