Zero emission buses: A holistic solution to battery electric and fuel cell technologies
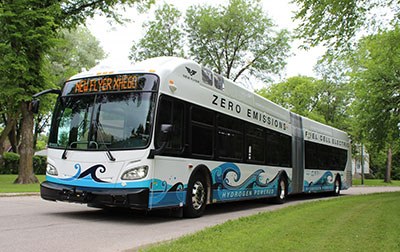
For the most part, the focus on true zero-emission technology has landed on one of two technologies:
Battery electric buses (BEBs) are driven by electric motors (with or without a transmission interface) and use energy from on-board battery systems. They typically use regenerative braking to recover vehicle energy and recharge while in service, with most recharging either performed overnight at a maintenance/storage facility or deployed en route to provide top-up charging throughout the day. This is considered a true zero-emission solution.
Like BEBs, fuel cell electric buses (FCEBs) contain electric motors, a battery system, and regenerative braking. The difference is that an FCEB also carries a hydrogen tank, providing fuel to a fuel-cell system that generates electricity and charges the on-board batteries. The FCEB typically does not require any recharging during the day and is only refuelled at the end of service, similar to current diesel fleets.
BEB or FCEB?
Both BEB and FCEB systems provide a zero-emission solution and have unique advantages and disadvantages. The option for bus operators is complex, and any solution is likely to require a nuanced, localized solution.
A simple comparator table of the main features will highlight the challenges.
BEB | FCEB | |
---|---|---|
Vehicle cost | $1.5 – $1.8 million/bus | $1.8 – $2.5 million/bus |
Vehicle range | Some claims approach 300 km but are severely restricted by the useable battery range, driver behaviour, and environment. In reality, the range could be as low as 40% of manufacturer claims. | Not as variable as BEB with most FCEB achieving ranges of 80% –90% of a diesel bus. |
Route implications | Shorter range and increased charging requirements require en route charging or for routes to be redesigned in shorter blocks to accommodate bus performance. | Similar to current diesel-supported routes. |
Fleet requirements | Because of range concerns, most operators are seeing a necessary increase in fleet size of 10% – 25%. | Same or similar to current diesel fleet needs. |
Refuelling/recharging time | Top-up fast charging can occur en route to extend total day range, but end of day charging will typically be around four hours. | Refuelling the hydrogen is typically < 20 mins per bus. |
Charging/fuelling system |
A wide number of site-specific options can be considered: • Fast charge/slow charge * Significant changes are needed to grid supply and power distribution on site. |
Fuelling is similar to a diesel process and hydrogen storage technologies have improved to reduce the need for specialist low-temperature storage systems. |
Infrastructure needs | Facilities will likely need major changes to power distribution and maintenance facilities to accommodate battery management and charging system. | Infrastructure changes are needed to be able to manage a lighter than air fuel system, similar to compressed natural gas facilities. |
Service resilience | In the event of a power outage service will likely be severely impacted. Consideration must be given to micro-grid solution and/or back-up generator systems. | similar to current diesel technologies. Additional hydrogen can be brought in if required. |
Fuel source | For a true zero-emission solution the full energy chain needs to be considered, including the source of the electricity generation (nuclear, CNG, coal, wind, or hydroelectric) in a total emissions calculation. | Hydrogen comes in color categories that denote the environmental impact of generation. The access to economic quantities of a source of green hydrogen is the biggest challenge for this option. |
The table is intended to show that hydrogen is a viable option in most cases IF the base fuel can be supplied in sufficient quantity and at a reasonable cost. It’s also worth noting that local environment, topography, fire risks, route design, and maintenance facility locations must also be considered.
The decision to transition and the direction to follow is both a strategic and political decision that agencies are currently debating. There is considerable vocal support for fleet electrification on a personal car basis as well as municipal fleets, but BEB technology trials highlighting the limits of lengthy routes, cold weather performance, long charge times, and battery life concerns are casting doubt on a single solution to cover all service needs.
The holistic solution?
Stable infrastructure can’t be implemented overnight; it takes time, commitment, and innovation. In this fast-paced industry, battery technologies are increasing in density, reducing in size, and improving range, and hydrogen generation is improving with increasing demand.
The work ahead includes government support for the technology and the vision to see the longer-term perspective, the development of hydrogen “hubs” to allow for efficient distribution, local support from transit agencies to examine hydrogen as a viable option, and vehicle suppliers to continue technology development.
The optimal approach is one of balance. Specific, local analysis of client needs is required before determining what and how to deploy the appropriate technology; it’s possible that BEB vehicles can be used for short routes or partial day service (school buses, for example), while FCEB technology is suited for full-day service, remote operations, and inter-city services.
Hatch possesses world-class engineering capabilities across the full hydrogen and electric vehicle and infrastructure landscape. From pilot to full-scale, we are actively involved in the development of the hydrogen economy and in investing in the future of a greener, cleaner planet. Contact us to find out how Hatch is continuing to grow our portfolio of projects and how we can partner with you to meet your sustainability goals.
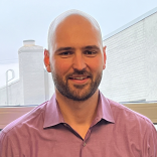
Daniel Lang, Ph.D.
Regional Director, Bus and Sustainable Transportation
Daniel Lang has 15 years of experience in vehicle, wayside infrastructure, systems engineering, and system safety aspects of bus, transit, and rail industries. He currently leads Hatch bus and sustainable transportation, which assists clients’ bus and paratransit vehicle engineering maintenance.
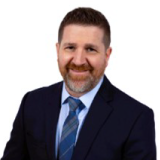
Jason Huck
Business Director, Transit, Alberta
Jason Huck is the Business Director of Transit in Alberta for Hatch. He is a project management professional and rail and transit systems subject matter expert who has planned and delivered major transportation infrastructure projects across North America. His 30 years of experience includes project and program management, advisory services, engineering and design, commercial contract development, as well as several years in construction and operational maintenance for a Class 1 railway. Jason has worked through all stages of project and program life cycles, from initiation through to implementation and close-out, and in a variety of project delivery methods such as Private-Public Partnerships (P3), Design-Build (DB), Progressive Design-Build (PDB) and Design-Bid-Build (traditional). He has a passion for developing highly motivated and efficient teams, which provides him with the ability to produce high quality technical solutions and deliverables for a variety of projects.