Are LFP batteries the key to meeting North American electric vehicle demand? How previously overlooked chemistry helps overcome headwinds to mass adoption
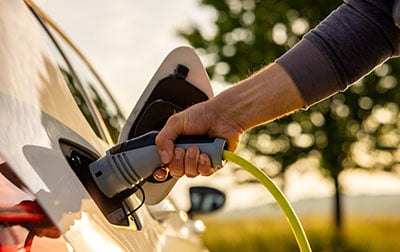
Some estimates suggest a compound annual growth rate of 40% – 50% over the next decade. Despite industry forecasts, headwinds remain for mass adoption of electric vehicles (EVs) in North America. First among these challenges is the supply gap of critical raw materials stemming from historic underinvestment in nickel and cobalt mining projects. This upward price pressure on raw materials used in nickel-based battery technology has been further exacerbated by geopolitical and ESG concerns (e.g., sourcing nickel from Indonesia, cobalt from the Democratic Republic of Congo, and material processing in China).
As constraints on critical mineral supply persist, the importance of utilizing alternative battery chemistries grows. One such chemistry that has gained momentum in recent years is the lithium iron phosphate (LFP) battery. Currently, North American electric vehicles primarily rely on a nickel-based chemistries such as nickel manganese cobalt (NMC) and lithium nickel cobalt aluminum (NCA) oxides. In contrast, LFP batteries offer an iron and phosphate chemistry, both of which are more abundant commodities. While LFP has been long thought of the dominant solution for stationary storage, a growing number of automakers in the west are beginning to consider it as a solution for their EVs. This presents an opportunity for automakers to offer cost-effective entry-level electric vehicles to the North American market.
LFP batteries also exhibit superior safety and stability profiles compared to NMC batteries, addressing a significant concern for EV consumers. The somewhat rare occurrence of NMC/NCA battery fires is due to their use of a flammable electrolyte and an inclination to thermal runaway. In contrast, LFP batteries are more resistant to thermal runaway due to their chemistry, which reduces the likelihood of a battery fire.
Another factor influencing electric vehicle adoption is range. While LFP batteries typically have a lower energy density—and therefore range—they can have superior charging properties and can be charged to 100% at a near-steady rate whereas NMC batteries are recommended to only be charged to 80% – 90% to reduce battery degradation over time. At current chemistries, this suggests the effective range of an EV using an LFP battery being comparable to that of an NMC battery.
Improvements in LFP manufacturing in North America have been slow due to costs associated with the licensing fee to use the LFP patent. The entity that held the patent for the manufacturing and use of LFP as a battery material entered into an agreement with the Chinese battery industry a decade ago. In the agreement, the entity would not charge Chinese OEMs a licensing fee for LFP that was produced and used in China. This arrangement granted China a significant advantage in both the operational expertise and experience in the production of high quality LFP batteries at scale. The recent expiration of these patents and licensing has paved the way for increased investment by North American producers in LFP. However, these producers will need to establish partnerships with experienced manufactures to effectively compete with China.
“LFP technology has the potential to shape the future of the electric vehicle landscape.”
Despite lower cost, better safety record, improved range, and the unique capability of LFP batteries to endure complete charge cycles (ranging from 0% to 100%, while batteries like NMC/NCA are commonly limited to partial charge cycles between 20% and 80%), the North American market has maintained a more conservative outlook on LFP adoption. These factors collectively will contribute to the potential demand for LFP-powered electric vehicles to constitute over 30% of new electric vehicle sales in the next decade. Industry developments over the next one to two years can be expected to shape the trajectory of LFP adoption.
For stakeholders across the electric vehicle value chain, awareness of leading indicators for LFP uptake can suggest implications for the industry’s steady state dynamics. Promising signs of LFP adoption can be observed through significant commitments made by North American original equipment manufacturers (OEMs) to utilize LFP batteries. For instance, Ford recently announced a licensing agreement with China's CATL to establish a LFP gigafactory, which comes as part of Ford’s diversified battery technology strategy. Tesla is also reportedly planning a new LFP battery-based gigafactory in Texas.
These developments highlight the growing interest in LFP as a viable alternative to NMC batteries. Additionally, new plans for LFP projects from large-scale cathode active material (CAM) producers would further validate a high-adoption scenario for LFP technology. Last year, Israeli chemical maker ICL Group announced a project to produce LFP cathode materials in St. Louis, Missouri expected to be operational by 2024.
Nano One, Gotion, Mitrachem and ICM Group have also announced respective LFP projects, signaling a widening industry focus on LFP investments. Major auto OEMs—which have taken an active role in shaping their battery supply chains—will be the largest driver in LFP adoption. GM, Mercedes-Benz, BMW, and Hyundai are among the companies exploring strategic partnerships, direct ventures, and other mechanisms in hopes of capturing the LFP opportunity in consideration of broader localization and raw material sourcing efforts.
LFP is also likely to become the dominant chemistry for battery storage. Unlike EVs, energy storage customers are primarily driven by cost and will be quick to adopt LFPs. Lower energy density of LFP batteries relative to NMC is less of a concern given space is not a limitation for energy storage applications. Increased development of lithium-ion batteries in the automotive sector has facilitated the cost competitiveness of similar batteries for stationary energy storage applications, and as that experience curve develops, this will lower cost and increase adoption into EVs as well.
Embracing LFP adoption also enhances battery supply chain stability for EVs and energy storage, benefiting both users and producers. Phosphate produced within North America for agricultural applications has the potential to expand into higher-grade products such as LFP while still maintaining its role in agriculture. To fully capitalize on the advantages for the US economy, the phosphate industry will need to expand capacities to include battery applications.
This also applies to the lithium supply chain where the US has only a small percent of the global reserves, and finding local sources has become a priority for the US government. The Arkansas Smackover lithium project is an example of localizing the battery raw material supply chain by utilizing the lithium found in the waste brine of existing bromine processing facilities. Another source of lithium found in the US is petrolithium derived from petroleum brine found in the salt solution brought to surface during oil and gas production. Domestic production of the raw materials found in a LFP battery presents a significant advantage as North America can achieve substantial domestic production through meeting the threshold set by the Inflation Reduction Act (IRA). Embracing LFP adoption will enhance battery supply chain stability for EVs and energy storage, benefiting both users and producers.
While still in an early stage, LFP technology has the potential to shape the future of the electric vehicle landscape, presenting a market opportunity for automakers as well as battery raw material and intermediate product producers.
How Hatch can help
Our battery market solutions team has worked with clients across the value chain—from raw material producers to battery and vehicle manufacturers— to evaluate, optimize, and implement strategic initiatives and major capital projects in consideration of federal funding opportunities and requirements. We take tremendous pride in bridging technical expertise with management consulting excellence and our collaborative approach for delivering actionable outcomes.
Authors
Mikael Lindgren
Regional Director,
Advisory, North AmericaJan Maceczek
Senior Consultant,
AdvisoryAravind Raman
Senior Engagement
Manager, AdvisoryNatasha Remtulla
Consultant,
AdvisorySiddarth Subramani
Principal,
Advisory