On the path to net zero in mining: It is the best of times
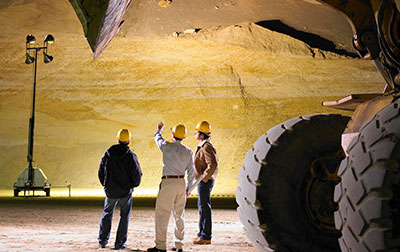
Herein lies one of the great dichotomies of the modern mining age: to achieve a net-zero future and successfully combat climate change, we need to scale and transform an industry that is notoriously capital-intensive, risk averse, highly dependent on fossil fuels, and can be beset with depleting high-grade resources, diminishing operational productivity, increasing debt, growing market volatility, and an unprecedented shortage of skilled labor.
However, as BlackRock CEO Larry Fink asserted in 2020, climate risk is investment risk. Significant capital and other financing mechanisms are now directly linked to achieve sustainable key performance indicators, and multiple governments worldwide have enacted policies and initiatives to enable significant emissions reduction for multiple sectors. But are these investments bearing fruit within the mining industry?
Have we started to see significant strides in overcoming barriers toward realizing a net-zero future for mining? Or is the industry floundering in producing and implementing viable decarbonization solutions? Will environmental, social, and governance transactions and commitments hamper the viability of future mining operations? Or is increasing investor pressure, carbon pricing initiatives, stringent regulatory policies and structured government incentives leading the mining industry down the only path available to it?
The short answer is yes to all! A great deal of innovation and collaboration is indeed taking place, propelling the industry to take on more risk than ever before. However, several technological, implementation, and economic barriers will prevent wide-scale and aggressive greenhouse gas emissions reduction, especially over the next decade.
Some mining operations will see significant on-site emissions reduction in a relatively short time frame, but those will be the exceptions, not the rule.
Being agile and adaptive in an age of commitments
Most emerging decarbonization solutions and commitments in mining are focused on eliminating Scope 1 emissions (direct emissions at source) and heavily reliant on securing renewable energy to reduce Scope 2 emissions (indirect emissions from purchased energy). Both scopes are a small slice of the pie when compared to Scope 3 emissions (indirect emissions produced both upstream and downstream of the mining operation), which requires more accurate and transparent reporting to help set definitive decarbonization targets for getting critical metals and minerals to market.
Achieving net-zero Scope 1 and 2 emissions by 2050 or sooner will require significant investment to prototype, test, and deploy viable carbon-free technologies and solutions. Two mining activities remain highly dependent on fossil fuels: mined material movement and comminution (i.e., crushing and grinding of mined materials).
The latter offers multiple opportunities for significantly reducing energy consumption and emissions: from circuit analysis and optimization to upstream drilling and blasting improvements in fragmentation, to preconcentration and ore sorting, to redesigning/replacing existing circuits and reducing the usage of grinding media. The primary challenge still remains the replacement of diesel-operated, heavy-duty mobile mining equipment.
The case for batteries: They don’t come free of charge
For most conventional, energy-intensive mining methods, diesel-operated mining equipment has been the backbone of the industry for many years, granting an operation the best possible combination of operational flexibility, productivity, and precision to combat commodity price volatility. More recently, underground mining has seen the proliferation of battery electric vehicles (BEV) to reduce equipment heat and diesel particulate matter generation, leading to potential reductions in ventilation costs and allowing operations to mine deeper.
However, even with a growing suite of commercially available electric equipment and chargers, there is no winning streak fallacy prompting the mass adoption of BEVs in underground mines. BEVs do not guarantee a positive economic outcome as they have many limitations, depending on their application, and their Total Cost of Ownership do not yet provide a competitive offering when compared to their conventional, diesel-run counterparts.
In the case of surface mines, which utilize much larger equipment than in underground mines, the deployment of BEVs becomes a forcing function, a catalyst toward implementing major changes in typical mining activities. It requires one to understand the ramifications of how limited state-of-the-art batteries are in terms of range, capacity, and charge rates. Large mining trucks, which represent the majority of Scope 1 emissions from hard rock mining operations, amplify this issue as their duty cycles require a great deal of energy.
Major equipment manufacturers are committed to making large surface mining trucks available in a variety of electric vehicle (EV) configurations within the next decade. Many emerging battery chemistries and technologies are being tested to curb the limitations presented above, but even the rollout of safer, fit-for-purpose, high density/high charge rate battery modules will do little to mitigate the increase in renewable energy demand on-site, the risks in supply chain disruption (due to the challenges in scaling battery manufacturing), or the potential for significant operational disruption when introducing stationary or dynamic charging infrastructures.
The case for hydrogen: The fuel of the far future
As demonstrated by Anglo American’s nuGen™ haulage solution, hydrogen-powered fuel cell-battery hybrid powertrains can effectively act as a means of onboard dynamic charging for the battery, significantly extending the range of large trucks. With the advent of ruggedized, liquid hydrogen onboard storage, a hydrogen fuel cell truck has great potential to match the range and operational flexibility of diesel-operated trucks.
Ultimately, the uptake of hydrogen usage in the mining sector becomes a chicken-or-egg argument. Hydrogen, notably green hydrogen, requires significant, regionalized production capacity and economies of scale to become as cost-effective as fossil fuels and expand the number of potential end-uses. In addition, establishing a hydrogen supply chain, notably for remote mine sites, may be more emissions-intensive than using fossil fuels.
Once on-site, hydrogen storage, compression, and refueling infrastructure will also be very costly and require an enormous footprint to offset the risk in supply chain disruptions. With green hydrogen production expected to grow exponentially over the next two decades, the levelized cost is expected to eventually become competitive with fossil fuels. It's simply a question of when.
The case for biofuels: More harm than good?
Next generation biofuels, notably renewable diesel such as hydrotreated vegetable oil (HVO), are slowly becoming the focus in multiple sectors for achieving low lifecycle emissions. Cummins' recent announcement certifying all their high-horsepower engines for unblended use of HVO illustrates the promise in utilizing a drop-in substitute for petroleum diesel, resulting in negligible impacts to engine performance and little to no modifications in fuel transportation and storage requirements.
But, like hydrogen, market availability and the means to sustainably source and produce significant biomass presents an enormous challenge, along with a great deal of debate over the resulting negative impacts to the environment and biodiversity. In addition, other sectors that are bigger emitters than mining, such as transportation and construction, will want to secure biofuels as part of their future to achieve net zero. So where does that leave us?
A staggered approach to decarbonization: You can’t have your cake and eat it too
While it is fully expected that traditional mining will be a thing of the past before 2050, there are no turnkey solutions (yet) guaranteeing the safe and economic transition to a fully decarbonized mining operation in the next decade.
Energy efficiency is the name of the game. As more resilient and cost-effective renewable energy pathways emerge, it becomes critical to:
- Introduce transitional mine decarbonization solutions into mining operations (e.g., Trolley-Assist, Autonomous Haulage, In-Pit Crushing and Conveying, EV with hybrid powertrains, biofuels, etc.).
- Gradually test and deploy emerging zero-emission solutions to improve and expand viable use cases.
- Invest in future technologies with the promise of moving beyond net zero (e.g., carbon capture and sequestration) and achieving other nature-based objectives.
With Hatch as your partner, a staggered approach to decarbonization can effectively and gradually add value to each mining asset. We have the experience and expertise to help introduce mature and emerging decarbonization solutions, unlock mineral resources, and optimize carbon reduction all while maintaining robust, safe, and profitable operations.
We've seen a marked growth in environmental stewardship in mining, with a lot of positive momentum toward reducing on-site water consumption, waste generation and land disruption. The same is happening when tackling greenhouse gas emissions, and while the journey won’t be easy, we’re confident the transition will ultimately strengthen the mining industry.
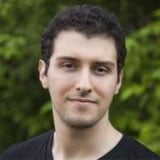
Michael Bobotis
Mine Decarbonization Lead, Mining
Michael Bobotis is a Mining Consultant, Engineer and Technologist currently headquartered in Montreal, Canada. During his tenure at Hatch, Michael has worked on multiple international mining projects as a project manager, engineering manager and mining specialist targeting multiple mining methods and commodities. As part of Hatch’s Climate Change and Digital initiatives, and in his role as Hatch’s representative on the Global Mining Guidelines (GMG) group's Leadership Council, Michael has endeavored to promote best practices as well as innovative technical and management initiatives for multiple mining operations, including both mature and emerging mine decarbonization, digitization and automation solutions.