Partnering for success: Engaging an EPCM for gigafactory development
This is where the EPCM (Engineering, Procurement, and Construction Management) approach should come into play.
Gigafactories and battery chemical manufacturing facilities are tied to a fixed electric vehicle platform start-of-production date, which typically takes three years from design to full operation. With battery cell design continually evolving and imposing modifications to plant equipment selection and layout, these highly complex projects require hundreds of contractors and subcontractors and can experience challenges meeting environmental and regulatory standards.
With this in mind, there’s a need for a highspeed, flexible delivery model to design and construct while keeping the highest standards in place throughout production. Engaging a leading engineering consulting company with specialization in the design of battery material and cell manufacturing processes and facilities, as well as battery recycling processes, is vital, and when it comes to gigafactory development, partnering with an EPCM organization offers several key benefits.
Traditional EPC (Engineering, Procurement, and Construction) may offer a fixed bid based on preliminary design. This “guaranteed cost” gives clients a false sense of security: the lump sum bid creates a sense of control by shielding the client from vendor selection and important decision-making processes, and providing the false sense that prices won’t change with the scope of the project.
In reality, the fixed price often becomes the lower limit of the plant cost, which often increases as change orders are submitted. We must not forget that transferring risk to the contractor isn’t for free, and often a 30% contingency is applied to the fixed price to facilitate this. Schedule is often delayed because the general contractor needs to appoint sub contractors as they lack a comprehensive design capability. This normally takes several months to accomplish, before any real design in outsourced packages is started.
EPCM offers a time and materials basis for detailed design, procurement, and construction management, which reduces cost by approximately 30% compared to traditional EPC models, as risk contingency is not added. Because the EPCM firm is able to initiate engineering of all aspects of the design on day one of the contract, the schedule is typically six months shorter than traditional models with improved transparency and control of deliverables. And if the client approves the EPCM provider as their agent and defines their responsibilities in the contracts, the EPCM provider can manage everything, an arrangement that offers more client engagement by putting them in the driver’s seat and giving them full knowledge and access to all service providers.
But how does this pertain specifically to gigafactories?
Broad expertise in engineering design
Designing a gigafactory requires an in-depth understanding of various engineering disciplines, including civil, structural, processing, mechanical, piping/ductwork, electrical, and instrumentation (automation) engineering. In-house experts in fire system, HVAC, environmental, utility, and facility designs are further supported by EPCM experts, ensuring development of the most efficient design while adhering to requirements and specifications. Using an EPCM company with a comprehensive capability is in essence the only way to obtain a fully-integrated design, which improves plant performance, maintenance, costs and schedule.
Effective project management
Building a gigafactory involves managing multiple stakeholders, complex timelines, and budgets. With effective EPCM integration, clients gain a single point of contact for the project manager throughout the entire process who assumes the responsibility of overseeing critical aspects of the project and ensures it stays on track, within budget, and meets the required standards. It should not be necessary for clients to deal with multiple companies; a holistic, one-stop-shop approach can and should manage all aspects of the project.
Procurement and supply chain management
An effective EPCM approach handles the procurement of materials and equipment essential for the gigafactory project. With a global network of suppliers, the approach secures high-quality raw materials and equipment at competitive prices while meeting schedule milestones, ensuring experience in supply chain management with large suppliers and a seamless procurement process. Appointing an organization that contains all the necessary expertise also allows for an integrated schedule to be assembled. This guides the entire planning of the project and ensures focus on the most critical activities. This is often not the case with the EPC approach, as the general contractor can lack expertise to assemble realistic schedules, and planning is typically done on an ad hoc basis (focusing on “putting fires out”).
Risk and safety management
It’s vital to partner with an organization that is adept at recognizing and mitigating the inherent risks that come with building a gigafactory. Teams need extensive experience in construction safety, environmental safety, and health safety, creating a secure working environment for the construction site while minimizing the risk of accidents. It requires best-in-industry performance in even the most challenging environments.
Choosing an EPCM partner
From expert engineering design to effective project management, procurement, and supply chain, risk, and safety management, EPCM ensures the project is completed on time, within budget, and to the highest standards. The complexity of building gigafactories necessitates the skills of an EPCM organization with credible and applicable experience, to ensure a successful outcome.
Organizations in the battery space who are considering an EPCM team for major capital projects need to find the right fit: an ideal blend of skills, leading practices, and technology to deliver projects on schedule and within budget. When choosing an EPCM team, several key factors must be considered:
- Comprehensive capability. The EPCM company selected should have to outsource (sub-contract) little to none of the scope. This enables the team to produce a fully-integrated design, which provides cost, schedule and plant performance benefits.
- Track record of successful projects. Evaluate the EPCM's track record of similar projects, understanding the reasons behind successes and lessons learned.
- Collaboration and team mindset. Look for an EPCM team that fosters a collaborative partnership, aligning goals and defining success for all team members.
- Health, safety, and environmental excellence. Ensure the EPCM team has a strong culture of safety, backed by demonstrable successes in health, safety, and environmental programs.
- Resource management. The EPCM team needs effective strategies for obtaining and retaining skilled personnel, crucial in a competitive labor market.
- Best-in-class systems and processes. Select an EPCM with proven best-in-class systems and processes to facilitate efficient project management and reporting.
- Low-cost, rapid-delivery sourcing capability. A strong EPCM team utilizes preferred supplier lists or offers their own preferred vendors to maximize cost-saving opportunities, while ensuring the schedule milestones are met.
- Global experience and reputation. Consider partnering with an EPCM with a global reach to ensure success in future projects on a global scale.
Major capital projects carry high stakes, and choosing the right EPCM partner is a critical decision. By considering these factors and finding the best fit for their needs, organizations in the battery space can ensure projects are delivered on time and within budget.
When it comes to gigafactory development and major capital projects, Hatch EPCM stands ready to ensure success through its expertise, collaboration, and commitment to excellence. Contact us to learn more about how we can help with your EPCM projects.
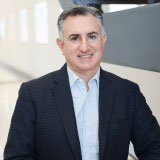
Mark Bellino
Global Sector Practice Lead, Manufacturing
Mark has over 26 years of experience in metallurgical engineering, study management and sponsorship, as well as flowsheet development and plant design. In addition, he has extensive experience in lithium, battery chemicals, and commercializing processes. He is the study manager and a consultant on the CTR Hell’s Kitchen lithium Project, the ERAMET MHP to Battery Grade Sulphates Process Study, and is deeply involved in CAM studies for NanoOne for both NCM and LFP chemistries. He is also the technical and project sponsor for the LiCycle Battery Recycling Hub Project, and a consulting advisor to the GM/POSCO Ultium CAM Project in Becancour, Quebec.