Balancing emissions and production: How IROCs revolutionize mining operations for a sustainable future
Today’s consumers seek a greener, cleaner, decarbonized future. They want solar panels, wind turbines, and batteries. They want electric cars and energy-efficient household appliances.
These technologies and products, however, require metals and minerals that must be extracted from the earth using conventional and unfavorable mining processes. By 2050, the demand for base metals and critical materials is expected to increase five-fold. More demand means more output, which means the mining industry will have to adapt to meet accelerating emissions goals.
Many global mine operators have committed to reducing carbon emissions by 45% by 2030 and achieving net zero by 2050. Achieving those goals will require the use of renewable energy, an industry paradigm shift, and – most importantly – adapting and upgrading Integrated Remote Operations Centers (IROC) to optimize and support decarbonization.
IROCs, which are already used by operators to access real-time data to monitor, control, and manage operations across multiple sites, can easily adopt new capabilities to support the complexities of emission-reduction technologies and processes.
In traditional mining operations, loading and hauling accounts for 50% of CO2 emissions. The remaining 50% is comprised of processing (21%), transport (18%), blasting (6%), blending/stockpiling (4%) and drilling (1%).
- How will mines produce more while reducing emissions? Leading approaches that miners must consider include:
- Process optimization: Using data that is already being tracked and monitored to create digital twins and machine learning models that accelerate efficiency and sustainable value
- Switching to renewable energy: Dynamically modeling the way clean and renewable energy. including wind, solar, and nuclear, feeds into energy networks and meets loading demand cycles
- Optimizing equipment management: Using data, analytics, and automation to optimize scheduling, routing, and maintenance
- Replacing diesel-fueled vehicles with hydrogen and/or battery-electric vehicles
- Rethinking mining methods (e.g., using pit-crushing and conveying to reduce the use of haul trucks, thus resulting in a net-reduction in emissions)
Such changes will no doubt increase the complexity of mining operations. Each has the potential to affect the dynamics of the value chain (e.g., create bottlenecks) and will require new operating procedures. However, continuous improvement is a fundamental feature of the IROC, which will be able to adapt to the unprecedented number of new technologies that will be introduced to enable decarbonization. IROCs are well-suited to:
- Support collaboration up and down the value chain: Promoting partnerships between external suppliers of energy and technology providers while responding to the demands of metals producers as they decarbonize
- Optimize performance and efficiency: IROCs can assist in creating solutions that reduce energy consumption, improve recovery rates, and make optimal use of waste streams
- Manage electrification and renewable energy sources: Collaborating more closely with gird operators and optimizing operations with more constraints and volatility
Of course, planning for sustainable mining is requisite. Accomplishing it is quite another. From an objectives standpoint, a sustainability mindset has to be embedded in the day-to-day operations. Production and energy plans must be aligned, and leaders to operators must understand the targets. They must work in a sustainable manner, not only optimizing the product for throughput and quality but for other aspects, including environmental, social, and governance (ESG) impacts. The expected increase in the demand for metal is likely to raise the risks of environmental and social harm. The integration of IROC data can lead to improved communication between stakeholders, investors, and community leaders and residents, fewer negative impacts, more local development, and increased compliance and safety.
Hatch has the expertise and experience to assist mine operators looking to balance emissions reductions and production. We offer specialized tools and accelerators, including our IROC Value Diagnostic, which enables clients to execute operations more effectively and achieve sustained value from their IROC.
During a recent zinc flotation project, our client was able to produce more metal without increasing emissions. Hatch used a digital twin and machine learning techniques to identify an impressive 0.8% recovery improvement in a short period of time.
There are similar opportunities to optimize your mining operations.
Whether you want to modernize or expand your existing IROC, or establish a new one, our proven approach can help put you on the path to a greener, cleaner, decarbonized future.
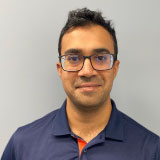
Anup Mistry
Global Principal, Integrated Operations and Remotization
Anup is a seasoned professional in the fields of Integrated Operations and Digital Transformation, with rich experience in the mining and metals industry. As a qualified GCC (Mine and Works) Mechanical Engineer with 15 years of industry experience, Anup possesses a strong operational background, having served as an Engineering Superintendent for a large coal mining organization for 7 years.
Throughout his career, Anup has been at the forefront of large-scale digital transformation programs for mining organizations worldwide. He has spearheaded the design, development, and implementation of iROC's, integrated planning & scheduling, predictive maintenance, and connected workforce solutions. Anup's extensive knowledge and expertise in shaping and deploying iROC strategies and roadmaps have consistently delivered sustainable value for his clients.