Powering tomorrow’s steel mills with nuclear energy
As the iron and steel industry moves to decarbonize its processes, a significant amount of carbon-free energy will be required, and nuclear technology is well positioned to be a part of the solution. By becoming an integral part of the steel mill, nuclear technology can be used to provide electricity, steam, and hydrogen, while also powering other GHG-reducing technologies.
The steel industry is an energy intensive and hard-to-abate sector and currently faces challenges with its decarbonization strategy. The traditional ironmaking process through blast furnaces relies on coke made from metallurgical coal as a key raw material for reaction and as an energy source, which generates significant amounts of CO2 and makes up the majority of GHG emissions from integrated steelmaking plants.
But with new nuclear technology at our fingertips, we can help. There are numerous synergies around combining nuclear power plants and steel mills, and this article discusses a few of the top pathways, and shows how nuclear energy can be a part of the solution to decarbonize the steel industry.
An overview of new decarbonization technologies
Many major steelmakers have identified direct reduced iron (DRI) as a pathway to significantly reduce GHG emissions. DRI utilizes natural gas—and hydrogen as an even lower emission alternative—to directly reduce iron ore without the need for melting. This pathway reduces overall GHG emissions when compared to the blast furnace route, and presents opportunities to further reduce emissions through hydrogen for DRI, electrical steel making, and carbon capture. The supply of emission-free hydrogen for decarbonized ironmaking is often constrained by the amount of clean electrical power for electrolysis.
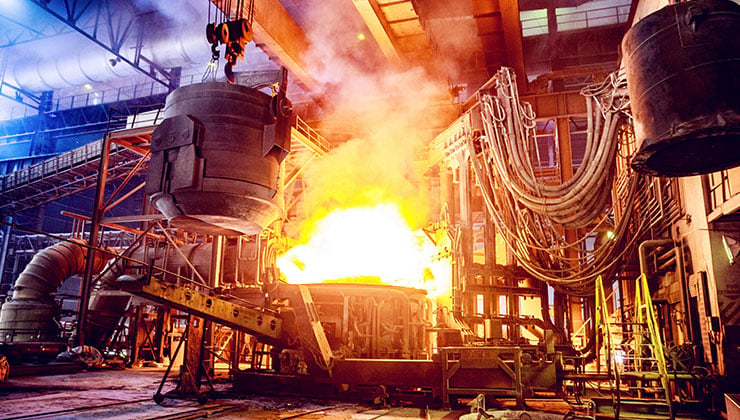
Traditionally, basic oxygen furnace steelmaking is utilized downstream of blast furnaces, in which oxygen is blown through molten iron to produce steel. While minimal electricity is currently required for this process, various DRI-based steelmaking pathways all require significant amounts of electrical energy. This includes the ubiquitous electric arc furnace (EAF) steelmaking process, as well as the Hatch CRISP+ DRI melting process, and the Hatch CRISP direct steelmaking process, which both use electric smelting furnace (ESF) technology. As such, access to large amounts of reliable, emission-free electrical power is urgently needed to help decarbonize the iron and steel industry.
Small Modular Reactors (SMRs) have been identified as one of the key technologies to aid in the global GHG challenge, with key advantages in reliability, flexibility of location, and scalability. By producing low-costs and zero-GHG electricity and steam, it can be envisioned that SMRs will be built near integrated steel mills, operating independently, and interconnected to the steel mill to provide electricity and steam while also supplying the local grid. SMRs provide reliable and constant power and steam that is difficult to achieve through solar and wind plants without a significant investment in energy storage.
Process electrification and carbon independence
Increased level of process electrification and fossil carbon independence is one of the dominant trends in the decarbonization of the iron and steel industry, and the advancement of nuclear energy can be an instrumental piece of the future net-zero emission integrated steel mill.
In this case, nuclear energy can be used to:
- Provide the plant with zero-GHG electricity and steam.
- Power electrolysis processes and locally generate emission-free hydrogen that can be directly used in the DRI process.
- Power carbon capture, utilization, and sequestration technologies can be integrated into the DRI process to further reduce emissions. (Carbon capture can also be used in blast furnace operation to capture emissions.)
- Link to storage capabilities including electric, hydrogen, and thermal storage.
- Provide additional synergies (e.g., utilize oxygen from electrolysis directly for the steel mill, power various carbon cycling/process gas conversion technologies).
SMRs and their role in the solution
While many of these technologies are new, many development projects and new-build applications are currently active. Together, they present a unique set of opportunities to reduce emissions from the steel industry. SMRs are emerging as a key part of the solution and can be combined with other technologies such as electrification, battery storage, and renewable energy to meet challenging GHG targets.
The size of the SMR is an important consideration and must be linked to the size and overall energy requirement of the steel mill and local grid. One should also consider the multiple possible uses of steam and electricity generated from the SMR beyond the steel making process that may co-locate with integrated steel plants, such as logistic and transportation, mining and mineral processing, hydrogen production/infrastructure, commercial and residential power, and district heating. There are also numerous opportunities to link SMR production to renewables, battery and thermal energy storage, electric vehicles and their infrastructure, and other clean technologies as a complete suite of solutions.
In this manner, highly dense industrial areas can utilize SMRs to meet the energy needs of multiple users in the form of low-emission nuclear power hubs similar to the concepts of renewable power/green hydrogen hubs. Conversely, remote areas could also see a great benefit with access to clean carbon-free power, new job opportunities, sparking new investments, and other synergies.
Contact us to find out more about the ways SMRs are well positioned to meet the needs of steel mills and to learn more about Hatch’s CRISP+ technology and the vision of providing reliable, zero-emission energy to the steel-making industry and surrounding communities.