Managing supply chains in the face of climate change risk: part 2
The Greenhouse Gas Protocol[1] has outlined the following:
Scope 1 |
Scope 2 |
Scope 3 |
Emissions are direct emissions from owned or controlled sources. |
Emissions are indirect emissions from generation of purchased electricity. |
Emissions are all indirect emissions (not included in scope 2) that occur in the value chain both upstream and downstream. |
To reduce scope 3 emissions while mitigating the risks that arise from new policies, it is essential for organizations to establish strategic relationships across their supply chain.
Currently, collaborations are focused on downstream supply chains, leaving room for improvement in upstream supply chains with suppliers and amongst competitors and complementary businesses. And for commodities such as steel, most of the emissions occur upstream during production.
This is why steel manufacturers upstream are now focused on working collaboratively to produce lower emissions products. Incumbents such as Algoma Steel are converting traditional blast furnaces to electric arc furnaces to lower emissions,[2] and newer entrants in the steel industry such as H2 Green Steel in Sweden are redefining how green steel is produced using a fully integrated, digitized, and automated plant that runs on fossil-fuel free electricity to produce steel.[3]
Moving toward a circular economy
Managing scope 3 emissions also requires a shift toward a circular economy. The circular economy is an economic system that involves eliminating waste and keeping products and materials in circulation through prolonging reuse, repair, remanufacturing, and recycling processes.[4]
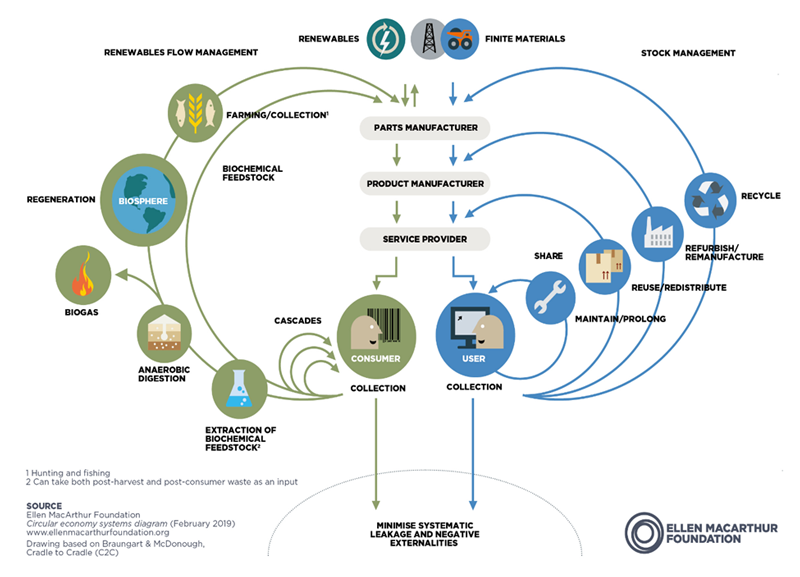
For example, the transition from fossil fuel vehicles towards electric vehicles (EVs) requires numerous metals in EV batteries. Since input metal materials are finite, an increasing number of initiatives to recycle these battery materials are being implemented globally. When companies procure these recycled materials for their products, this diminishes overall GHG emissions that would have been emitted from mining and processing new metal materials.
What strategic collaborations are required across the supply chain to support a low-carbon future?
The carbon life cycle of a product begins with the extraction of raw material and continues through manufacturing, distribution, maintenance, and end of life.
In design: It’s important for organizations to understand the carbon footprint of products and to create design cultures that prioritize product design, improvements, and the testing and piloting of technologies that contribute to a lower footprint. Designs should incorporate circular economy objectives such as prolonging materials through improved material composition, reduced scrap-waste, and designing with parallel industries for the remanufacturing of materials.
In manufacturing: Manufacturing plants can be co-located so that otherwise wasted by-products from one product may become valuable inputs to another. Academia-industry partnerships are driving innovation in advanced engineering and mining solutions. For example, the Advanced Sustainable Manufacturing Technologies (ASTUTE) provides knowledge exchange between industry and academia through collaborative research projects.
In distribution: Transportation, warehousing, and distribution of material plays a fundamental role in maintaining a stable supply chain. Given the dependence of transportation vehicles on fossil fuels, this is an area that presents significant emission reduction potential. Initiatives such as re-designing distribution networks, looking at bringing suppliers closer, optimizing packaging volume and weight, and reducing vehicle-fleet carbon intensity are key to reducing emissions.
In maintenance: There are also opportunities to reduce a product’s carbon footprint by developing processes, maintenance, and repair strategies that optimize the life of equipment by extending or repurposing its life. Organizations that have undertaken these types of initiatives estimate that rebuilding their equipment has 70% less emissions than replacing with new.[5] This type of asset strategy requires collaboration with vendors to develop and manufacture equipment that includes components that allow for rebuilding.
End of life/second life: In mining, whether a site has been contaminated, uncontaminated, or reached its reclamation state, there is an opportunity for further use and economic opportunity.[6]
What collaborations need to be established to achieve net zero by 2050?
Many organizations are intending to achieve net zero GHG emissions by 2050—an ambitious target that will require reimagining and transforming supply chains. Net zero by 2050 is the international scientific consensus that GHG emissions throughout a company’s value chain must be balanced by removals to remain consistent with 1.5 degrees Celsius warming of the planet. These goals mean that the traditional toolbox of efficiency gains will have to be expanded by accelerating innovative technologies, building symbiotic relationships, and leveraging nature-based solutions.
Accelerate technology:
- Establish a project management office for decarbonization initiatives that have a mandate and the resources to drive decarbonization projects
- Adopt new software that provides the required information to track emissions across the supply chain
- Manage and develop mitigation plans to reduce early adoption risks
- Implement 3D printing technologies so parts can be manufactured for local end-use
- Plan to electrify GHG-intensive assets
- Switch from using fossil fuels to low-carbon alternatives such as biofuels, green hydrogen, and electrification.
Build symbiotic relationships:
- Establish alliances with competitors or complementary industries to reduce emissions and better manage costs
- Leverage government clean-technology development incentives (e.g., Sustainable Development Technology Canada (SDTC))
- Nurture eco-conscious business innovation incubator programs and support local initiatives in your ecosystem.
Leverage nature-based solutions:
- Accelerate the implementation of nature-based solutions to reverse natural resource degradation and reduce biodiversity loss while sustaining economic development through mobilizing financial investments
- Carbon dioxide sinks to remove atmospheric GHGs that can be implemented in various natural systems. This can include activities such as in the reclamation of a mine site beyond what is legally required, in order to reforest the land that was previously the mine site.
How can we help?
Hatch can provide end-to-end supply chain decarbonization solutions by developing supply chain decarbonization alliance framework, simulating and modeling different scenarios to assess impact on operations, developing a plan to replace and incorporate new technologies while mitigating risks, and working with clients to develop supplier diversification and selection strategies.
By basing our service offers on decision levels and timeframes, we identify specific climate risks and form innovative solutions and supply chain collaborations accordingly. This type of holistic consideration includes strategy and transformation road mapping, transaction support, carbon footprint and risk assessments, medium- and long-term operational plans, and complete asset management and operational efficiency.
Contact us to find out more about how Hatch can help with your supply chain decarbonization needs.
[1] Greenhouse Gas Protocol
[2] 'Green steel' captures attention of Canadian steelmakers | CTV News
[3] Green Steel production — H2 Green Steel
[4] Ellen Macarthur Foundation
[5] The Truck Keeps Rolling (teck.com)
[6] ccsi-circular-economy-mine-land-potential.pdf (columbia.edu)
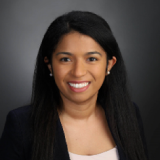
Grecia Pacheco
Consultant, Advisory
Grecia is a goal-oriented and customer-centric consultant with over 8 years of experience working in fast-paced environments. Throughout this time, she has had the opportunity to work in the mining industry and contribute to projects in supply chain, operations, maintenance, asset management, and marketing, helping organizations improve their processes and save millions of dollars in inventory. Grecia holds a Bachelor of Science from the University of Montana, an MBA from the University of Alberta, and is an APICS certified Supply Chain Professional.
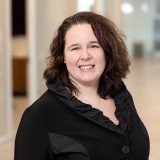
Julie Bourgault
Principal, Global Supply Chain Leader
Julie is an experienced advisory leader with more than 20 years of consulting and industry experience which spans multiple industry sectors including mining, aerospace, manufacturing, power. Her professional experience includes strategic vision, operational efficiency, large transformation projects, as well as lean implementation. She focuses on helping clients think and implement their business model and ways of working to rapidly align their strategic vision with day-to-day operations. She is recognized as a collaborative leader that manages complex program and ensures lasting results. Prior to joining Hatch, Julie was an associate partner at Ernst & Young in Canada.