Disruptive technological advancements in the oldest engineering discipline
Enter 3D machine control. 3D machine control is a grade control system that utilizes cutting-edge earthmoving systems that put design surfaces, grades, alignments, and other design features inside the cab of heavy earthmoving construction equipment, hand-held displays, and GPS rovers. These systems adopt a combination of either GPS, GPS and laser, or GPS and construction total station technology to accurately position the earthmoving machinery’s blade or bucket in real-time, eliminating the need for dedicated surveyors, staking out the ground, and significantly reducing exposure of personnel around big pieces of heavy moving equipment.
Compared to conventional standalone 2D engineering plans, creating 3D civil models results in easier implementation of changes, higher accuracy, and prompt error detection. Therefore, the use of civil models and 3D machine control systems is a win-win solution for the construction contractor, the engineering consultant, and subsequently our clients.
Hatch’s DES Civil Site Development (CSD) team has developed a standard guide that outlines the procedures required to develop and deliver civil models for direct utilization in earthworks 3D machine control products during construction and ensures the below objectives are realized:
· Civil model-associated design surfaces and other features are wholly consistent and include all necessary and relevant data-centric attributes that enable utilization of machine control technology.
· The basis and framework of the model, together with its objects, is compatible with existing industry machine control equipment to facilitate its direct interpretation and application during construction.
· Minimizes errors and redundancy.
· Significantly reduces production of 2D deliverables.
· Streamlines checking, sealing, and issuing digital civil model transmittals.
· Enables better integration with other engineering disciplines as part of Hatch’s Digital Project Delivery program.
A fundamental building block of a surface used in civil 3D modeling is the Triangulated Irregular Network (TIN) which is the format used to transmit spatial ideas into something that can be transferred to site for civil works, such as site grading. A TIN consists of triangle definitions that have x, y, and z coordinates for each of the three corners of each triangle. For the purpose of direct utilization of civil models into 3D machine control software, the civil TIN model accuracy is considered essential when laying out roads and graded pads construction, especially with curves, crests, and open channels. The designed TIN surfaces must accurately define slope changes and other areas with large gradient changes, such as ramps modeled with finer triangulations at curves. Civil gravity piping models and buried utilities models should also be modeled accurately to reflect the intended depth through the pipe/utility alignment. A prerequisite to an accurate design model is to acquire a high-accuracy site survey instead of relying on scanned, traced contour lines or other low-accuracy surveying methods.
In addition to the above, for civil site grading design, it’s crucial to model both the finished grade and subgrade surfaces Digital Terrain Models (DTMs). The subgrade is the interface between the substrate and superstructure. Since the latitudinal slopes of the subgrade are sometimes not parallel to the surface covering, a subgrade DTM should be created and can be derived from the finished grade DTM. It’s also recommended that breaklines are displayed as lines, as they help the earthworks machinery operator to better read the slope change, which is difficult to decipher based solely on the DTM triangulation.
The new CSD guide will enable our civil professionals to transfer the developed engineered design directly to the construction crew operating the earthmoving equipment on site. This new approach facilitates the design engineer goal to generate an end-product that conforms to the engineering design intent in a highly effective and streamlined process. Afterall, the design team is the one working closely with our clients during the engineering phases to understand their needs and have the required synergy to produce an optimized engineered solution to meet them.
Welcome to the future.
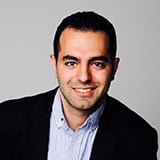
Yassir Hamandi
Senior civil engineer , DES - Civil Site Development
Yassir Hamandi is a senior civil engineer at Hatch, with over eleven years of experience. He successfully handles complex multi-disciplinary projects in the mining, energy, and municipal/infrastructure industries, working with clients throughout all project stages from concept to detail design, construction management, and quality assurance.