Digital Twin: more than a buzzword
TM: So how do we continue to apply Digital Twin technology to industries like metals and mining without getting caught up in the hype and jargon?
YZ: The secret is in focusing squarely on the value delivery and improvement opportunities. For our metals and mining clients, we usually zoom in on asset life and/or process stability. A value focus and drawing a line between outputs of the twin, operational actions, and KPI improvement is the only way to meaningfully apply a twin.
Let me give you an example: many pyrometallurgical processes are operating at a very high temperature and/or pressure, which makes it impossible to directly measure their internal states, such as metal temperatures or levels. Without access to critical process information, operators often get blindsided, leading to potential safety risks or unplanned downtime. In a recent project, our team commissioned a Digital Twin to make these internal states transparent to operators so that they can make timely decisions accordingly to plan casting operations and avoid process upsets. As a result, a more stable and consistent operation is achieved with a significant decrease in non-casting time.
In addition to value, long-term maintainability is another factor in realizing the true value of Digital Twins. We’ve made significant efforts in ensuring that Digital Twins are a true representation of their physical twin over time and their outputs are trustworthy through continuous monitoring of data quality, the introduction of the model quality index, development of model self-learning capability to avoid plant-model mismatch over time, etc. These best practices will continuously bring added value to plant operation and sustain long-term success.
TM: The Digital Twin market has grown quickly over the last few years. Many technology vendors are offering different Digital Twin products. As an industrial practitioner, what are some of your suggestions to end-users?
YZ: If we apply the 3I Digital Twin framework to these commercially available products in the market, most of them are focused on integration platforms and lack intelligence as the core component of Digital Twins. A successful Digital Twin solution must have the right ingredients, meaning design expertise, know-how, and/or operations expertise of its physical twin.
At Hatch, we have more than sixty years of experience in the design of electric arc furnaces for the non-ferrous industry. Such experience, together with all design models, is incorporated into the furnace Digital Twin design process, in which furnace performance KPIs, furnace integrity monitoring, structure and binding system, electrode management, production planning, etc., are holistically taken into account to ensure the Digital Twin benefits are delivered to end-users successfully.
TM: Among many different client organizations, who do you often see in the driver’s seat in successful Digital Twin execution?
YZ: I’d say it depends. Digital, innovation, technology, or operations teams were a good starting point when we first started looking to deploy complex process twins. My experience has however been that the most successful implementations are enabled by deep collaboration between digital and operations, maintenance, and production planning teams. For a Digital Twin to sustainably create value, those in the organization who can benefit and use the twin must be brought together during the twin’s planning and setup phases. During this process, sponsorship from a client’s senior management also plays a significant role.
TM: Thanks for your thoughts here, Yale. Are there any further plans you’d like to share with the readers?
YZ: I’m fully convinced that Digital Twins are a disruptive technology that will bring significant and tangible value to the heavy industry. I understand that there can sometimes be confusion or suspicions about the Digital Twin technology in the current market, but those concerns are likely caused by inappropriate planning, expectations, design, development, and deployment.
Stay tuned for an upcoming blog where I take a deeper dive into lessons learned!
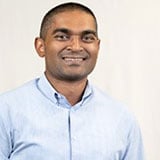
Thessy Moodley
Regional Director, Digital, Africa, Europe and Middle East & Integrated Operations Consultant
Thessy brings over fourteen years of post-qualification experience as a control and instrumentation engineer in various industries for local and international EPCMs and management consultancies. He has been involved in the design, engineering, optimisation, tuning, and commissioning of industrial control, automation systems and instrumentation for projects in the pulp and paper, bulk materials handling, oil and gas, and smelting industries He has augmented his technical expertise with the management and review of strategic contracts, cost savings initiatives, business strategy development, technology and digital strategy development and maturity assessments for the mining and metals industry. This has allowed him to hone in on value creation through the application of technology and digitalisation.
Under his leadership, Hatch’s Digital team in the region executes industry 4.0 based projects in optimization, advanced planning and scheduling, digital value chains, integrated operations, and Digital Twins for the metals, energy, and infrastructure sectors. Thessy holds a master’s degree in control engineering and is a registered professional engineer.
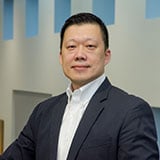
Yale Zhang
Principal Consultant , System Integration & Interoperability, Digital
Yale Zhang is a professional engineer with over twenty years of experience in process system engineering and digital technology consulting and development within the metals and steel industries. He has worked with clients across North and South America, Europe, China, and Southeast Asia. His technical expertise spans the areas of intelligent decision optimization, data analytics, discrete event simulation, and advanced process control. Yale’s current role at Hatch is to lead the advancement of Digital Twin technology to deliver actionable visibility and insight into business and plant operations.