Reducing our carbon footprint in mining and metals: how to build a decarbonization strategy and roadmap
The question is how to develop an achievable plan that creates value and delivers on a realistic target for greenhouse gas (GHG) emissions reduction. Each facility is unique, meaning there is no one-size-fits-all solution. The answer is a proven methodology that considers all aspects of a facility, identifies and evaluates all potential opportunities to reduce emissions, and prioritizes the solutions in a way that facilitates implementation. Ultimately, the outcome is a roadmap with attainable targets supported by credible, viable projects.
Developing a decarbonization roadmap
To help our clients develop decarbonization strategies, we deploy a proven methodology built around the concept of levelized cost of conserved carbon (LCCC) and the abatement cost curve. This powerful tool allows us to identify each opportunity's abatement potential and cost, compare them against other projects, and prioritize those that will form the roadmap.
The following activities outline the methodology in the context of an aluminium smelter; however, this methodology has also been successfully applied to alumina refining and other metal-producing plants, such as base metal smelters, refineries, and integrated steel mills.
1. Identifying opportunities
The first step is a thorough review of the facilities to set the boundaries. As an integrated team reviews each part of the facilities, three questions are asked: How can the existing process be optimized or modified? What other technology can be applied? And, what end-of-pipe solution can be employed? A deep level of expertise is required to identify and evaluate the opportunities. Some areas will require specialty expertise depending on the requirement, such as in aluminium smelting or power generation.
2. Evaluation and costing the opportunities
Before first-pass screening, the GHG emission reduction potential is calculated followed by a high-level estimate of capital and operating costs. There will be multiple opportunities identified for various parts of the plant and a high-level scope is defined to identify what is required to implement the changes, including associated costs. The estimate includes key cost elements from vendors, engineering, construction, and the owner.
3. Screening the opportunities
During the first-pass screening phase, initiatives are mapped to specific emissions sources and evaluated considering implementation barriers and risks. Note that this should not be done with all opportunities; only those opportunities that pass this evaluation are moved forward to the next phase.
4. Developing the LCCC
To include both the capital investment and the operating costs in an evaluation, the LCCC is calculated. This method puts both parameters on equal ground to identify and prioritize those projects that add the most value and should be implemented first. The calculation of LCCC is done using a discounted cash flow model with built-in financial criteria set by the owner.
5. Establishing the abatement cost curve
Once the list of opportunities is reduced to a selection of projects with identified levelized costs, the projects can be assembled in an abatement cost curve. The abatement cost curve maps projects from the most negative value (those that save money) to the highest positive value against the amount of CO2 that will be abated. This plot provides a clear, visible representation of which projects will have the greatest impact.
6. Evaluating the potential projects
Evaluating the potential abatement projects is an iterative process. Not all projects may need to be implemented for a facility to achieve its target. The evaluation identifies which projects should be selected and the level of GHG reduction over time. The final selection identifies all the pieces of the decarbonization roadmap.
7. Building the decarbonization roadmap
The selected projects can now be placed along a timeline that shows the steps that will be taken to achieve the target GHG emission reduction. The timeline also shows the profile of investments needed to implement the projects, barriers, and enablers that need to be monitored as appropriate, and key decision points along the way. This step is an important deliverable that can be communicated to key stakeholders.
The roadmap is dynamic and iterative. After projects are implemented their impact is measured and, depending on the results, the roadmap may need to be adjusted— adding projects that were not initially selected, or scaling down those that may no longer be required.
8. Implementing the projects
By doing our homework early, we are more likely to be successful when it comes to implementation. If scoping is done correctly during the development stage, high priority projects can start right away. The scope of work is confirmed quickly, and an execution plan can follow immediately, allowing for a smooth implementation process between the owner, the engineering firm, and original equipment manufacturer.
Conclusion
A structured methodology is the best way to develop a credible decarbonization strategy based on an actionable roadmap. It clearly identifies, screens, and prioritizes projects that, once implemented, will help an organization meet their GHG reduction targets. A critical success factor is accessing people with deep knowledge of processes and project delivery; it sets the roadmap up for success at the beginning of the implementation phase. And, it does not stop there. Once the target is in sight, the process will likely start again with a new, more aggressive target to achieve our collective net-zero ambitions.
Find out more!
Dr. Trevor Bergfeldt and Stephan Broek presented Identifying & Setting Priorities through Road Mapping of Decarbonization Projects at the Greener Aluminium Online Summit on June 2, 2021. Watch the recording of this webinar on-demand!
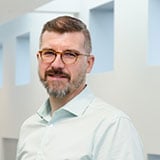
Dr. Trevor Bergfeldt
Global Director, Decarbonization & Sustainability, Metals
Trevor brings twenty years of experience in project delivery, business and technology development, operations management, resource efficiency, and circular value chain creation. He started his career with a leading multinational resource company working at one of the largest fully-integrated base metal smelters with roles in applied research, technical support, production engineering, and project management. He spent the next decade leveraging that expertise to deliver innovative technical solutions to sustainability challenges in management and executive roles with global process equipment and cleantech suppliers. Trevor joined Hatch in 2019 to help fight climate change by accelerating the industry’s transition to a carbon-neutral economy. Trevor holds BSc and PhD degrees in Chemistry from the University of Saskatchewan.