On the path to zero emissions: how the mining industry is working towards GHG-free surface mining
The path to net-zero carbon emissions is a global, multi-sector challenge and developing road maps to achieving that goal requires industry commitment, innovation, and new technological solutions. The challenges to achieving decarbonization road maps in the mining industry need to be tailored by operation, addressing the key pillars of decarbonization: energy efficiency, hybrid power, microgrid integration, alternative vehicles, mine design, and process adaptation to alternative energy sources. Specifically, one of the critical challenges that needs to be addressed is the reliance on diesel fuel.
The mining fleet is one of the industry’s primary sources of on-site greenhouse gas (GHG) emissions. Mobile mining equipment at a surface mine can account for up to 30 percent of on-site GHG emissions—or up to 80 percent if the mine doesn’t have contiguous smelting or refinery facilities. Large mining haul trucks can represent more than 50 percent of the total surface mobile fleet’s GHG emissions.
In 2018, the International Council on Mining & Metals (ICMM) launched the Innovation for Cleaner Safer Vehicles (ICSV) initiative, which brings together twenty-seven of the world’s leading mining companies and nineteen original equipment manufacturers to accelerate innovation in the development of a new generation of mining vehicles and to improve existing vehicles. ICMM’s goals are to reduce GHG emissions, emissions of diesel particulate matter, and vehicle interactions for improved safety. The ICSV initiative aims to achieve GHG-free surface mining vehicles by 2040, tackling the main source of Scope 1 emissions, which are direct emissions from owned or controlled sources (i.e., emissions from the surface mining fleet).
How do we get there?
In collaboration with the ICSV working group, we recently completed a study to help define the way forward. The objective of the study was to determine implementation pathways to achieve ICMM’s goal of zero-emission surface haulage trucks. To do this, we evaluated seven types of mining applications representative of ICMM member company surface mining operations/haulage profiles and analyzed technologies that could support reduction of their GHG emissions.
A multidisciplinary and cross-sectoral team approach was paramount to providing guidance on decarbonization pathways as mining companies with different types of surface operations continue to strengthen their commitments to climate action. Our methodology combined engineering and mining knowledge with technology identification and evaluation, investment and business planning opportunities, sustainable financing, advisory, and environmental/social impact best practices.
In the first phase of the study, a static energy profile simulation model was developed. This model enabled the analysis of energy consumption and GHG emissions in a full duty cycle of mining haul trucks for the following seven types of surface mining applications:
- Long flat hauling (up to 30 km)
- Short flat hauling (up to 5 km)
- Downhill long hauling
- Uphill long hauling
- Downhill short hauling
- Uphill short hauling
- Hauling (up to 5 km)
Once profiles were developed for each of the applications, it was important to ascertain the present and future viability of GHG abatement technologies to support a new generation of mining trucks. The study analyzed the current landscape of commercially available and emerging technologies that could support either significant reduction or complete elimination of surface haulage truck GHG emissions.
We looked at transformational technologies only and, per ICMM’s mandate, did not consider alternative means of material handling (e.g., in-pit crushing and conveying or Rail-Veyor). Retaining all the advantages of conventional surface mining trucks will be paramount in ensuring that a successful decarbonization pathway can be achieved for as many surface mining operations as possible.
In addition to GHG abatement strategies, capital expenditure and operating expense estimates and levelized cost of carbon conserved calculations were developed for each of the following transformational technologies as applied to surface mining trucks:
- Use of Biodiesel B100
- Hybrid electric vehicles (HEVs) with Biodiesel B100
- Battery electric vehicles (BEVs) - non-catenary
- Catenary BEVs (i.e., paired with trolley-assist)
- Hydrogen fuel cell electric vehicles (FCEVs)
What did we learn?
While these technologies present definitive pathways towards rendering a surface mining truck’s duty cycle free of GHG emissions, each pathway presents different advantages, disadvantages, opportunities, and challenges when applied to the different surface mining applications. Numerous aspects related to truck configuration, operational context, and truck performance directly affect both the viability of the technology pathway and the baseline assumptions required to estimate GHG abatement costs. Considerations include:
- Biodiesel B100: the viability of Biodiesel B100 is contingent on the integration of optimized engine designs; the availability, supply chain, and logistics of obtaining B100; and the competitive unit cost of B100 v.s. diesel.
- HEVs with Biodiesel B100: HEVs with B100 require similar considerations as above, with the added necessity of higher battery energy densities and lower recharge times to mitigate impact on truck fleet productivity and site infrastructure requirements.
- Non-catenary BEVs: in addition to lower battery costs and higher energy density requirements, BEVs without trolley-assist require greater charging infrastructure requirements. In the context of competitive electricity costs and a predominantly downhill-loaded haulage profile (i.e., regenerative braking), this technology pathway presents a high economic potential for mining operations.
- Catenary BEVs: in addition to similar considerations as non-catenary BEVs, BEVs with trolley-assist integrate a mature technology that, if the catenary infrastructure is relocated too often, can be cost-prohibitive. However, for uphill-loaded haulage profiles where catenary infrastructure can remain in place for years on end, the advantages of catenary BEVs (e.g., reduced charging requirements and higher speed performance uphill vs. non-catenary BEVs) can be fully realized.
- Hydrogen FCEVs: compared to BEVs, hydrogen FCEVs present with a clearer pathway to integrate hydrogen fuel cells and batteries into large, ultra-class haulage trucks. While presenting lower energy efficiencies from grid to wheel compared to BEVs, FCEVs (depending on the powertrain configuration) have a longer range than BEVs, which mitigates the impact of truck fleet productivity.
While a great deal of uncertainty remains in the evolution of related mining truck technologies and in the implementation challenges for the different GHG abatement solution pathways, it’s uncontested that surface mining operation paradigms will need to be adjusted to accommodate the inclusion of GHG-free surface mining trucks and ensure high productivity and operational flexibility, and low total costs of ownership.
This blog is based on the presentation “Identification of implementation pathways for zero emission surface haulage trucks to reduce Scope 1 GHG emissions” by Michael Bobotis at Canadian Institute of Mining, Metallurgy and Petroleum's 2021 Virtual Convention & Expo.
Click here to read Canadian Mining Journal's article "Harnessing hydrogen: Miners explore the use of hydrogen-powered haul trucks" featuring insights from Michael Bobotis.
To find out more, please click here to contact us.
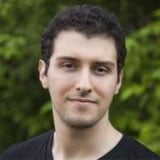
Michael Bobotis
Mine Decarbonization Lead, Mining
Michael Bobotis is a Mining Consultant, Engineer and Technologist currently headquartered in Montreal, Canada. During his tenure at Hatch, Michael has worked on multiple international mining projects as a project manager, engineering manager and mining specialist targeting multiple mining methods and commodities. As part of Hatch’s Climate Change and Digital initiatives, and in his role as Hatch’s representative on the Global Mining Guidelines (GMG) group's Leadership Council, Michael has endeavored to promote best practices as well as innovative technical and management initiatives for multiple mining operations, including both mature and emerging mine decarbonization, digitization and automation solutions.